The Appeal of Storing Heat (in Bricks)
Thermal Storage vs. Alternatives
Thermal storage is inexpensive and has moderate energy density but remains niche. Fossil fuels excel at producing heat, and storing that heat adds unnecessary cost. Oil contains ~40x more energy per unit mass than refractory bricks can store.
A handful of startups are taking a second look at thermal storage with the rise of variable renewables. It is ~50x cheaper per kilowatt hour than lithium-ion batteries. Any mass can store heat, often with minimal physical change. Electrochemical batteries are complex devices requiring pricey materials and elaborate manufacturing processes that increase cost. But batteries can efficiently store electricity while heat is expensive to convert back into electricity. Thermal storage can beat batteries by providing heat or operating for longer durations.
Industrial heat makes up 26% of global final energy usage, providing ample opportunity for thermal storage.
Pumped hydro storage and compressed air storage are other technologies deployed at scale. Both have abysmal energy density. Finding suitable locations is challenging. Thermal storage is ~100x more dense, on par with electrochemical batteries. It is compact enough to fit near factories and other users.
Thermal storage can be compelling when matching cheap electricity from renewables and users that require heat.
The Virtue of Bricks
The ideal heat storage material is a solid with a high melting point, doesn't fall apart with thermal cycling, has good heat capacity, and is cheap. The few liquids that can handle high temperatures have unpleasant properties. Solids can act as the heat exchange interface, lowering costs when heating gases. A higher melting point increases storage because the energy stored is the temperature delta multiplied by the heat capacity. Increasing the maximum temperature is necessary for applications like cement kilns. Many solids crumble under thermal stress, shortening system life, so materials must be stable.
Refractory bricks made of silicon dioxide and aluminum oxide are a classic solution. Competing materials like loose sand, crushed rock, or graphite have lower heat capacities, melting points, and densities. Graphite has further issues because it tends to oxidize at high temperatures. Mixtures like aluminum oxide and silicon dioxide in bricks store more energy in less space and mass while still being dirt cheap and stable.
The Evolution of Brick Heat Storage
Blast Furnaces and Cowper Stoves
A key advance in iron production was "hot blast," or preheated air. Hot inlet air allows the furnace temperature to increase and fuel consumption to decrease. Another advance was the Cowper Stove. They are giant heat regenerators that capture waste heat from the exhaust and use it to preheat fresh air to create the "hot blast."
The regenerators are usually a tower filled with bricks arranged in a checkerboard fashion. A blast furnace might use 3-4. Exhaust air flows through the bricks, heating them. The exhaust is switched to another regenerator once the bricks are hot. Operators blow fresh air through the hot bricks until they cool. A Cowper Stove-style regenerator usually goes through 24 cycles per day and has a service life of 30 years, thanks to many incremental improvements in brick manufacturing. The cumulative storage capacity of these systems is in the gigawatt hours.
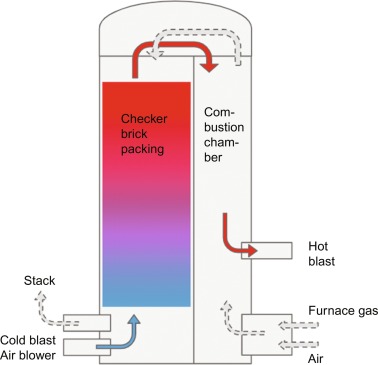
Cowper Stove Source: Sciencedirect.com
The application favors brick towers over traditional heat exchangers for several reasons. High temperatures paired with acid gases make material selection a challenge for heat exchangers that are typically metal, but the bricks are very durable. Gas-gas heat exchangers can be enormous because gases have lower thermal conductivity. The checkered bricks provide extensive surface area for heat transfer. Heat exchangers are more efficient when fluid velocity is high, but this increases pressure drop. The brick towers have very low-pressure drop. Facilities can use inexpensive blowers in place of pricier compressors.
Brick heat storage improves blast furnaces and can operate in an environment that challenges traditional heat exchange methods. Hundreds (or thousands!) of years of brick technological development make them an asset for future thermal storage systems.
Heating Bricks With Toaster Wire
Early concepts for using bricks to store renewable electricity deviated from existing designs as little as possible. A blower would push air through an electric heater and past the bricks, making them hot. The system could run in reverse to recover the heat. The hot air would heat a process directly or produce steam in a boiler.
The challenge is that electric heaters for air are large and expensive. Heating the bricks with air makes sense when it is waste heat from a furnace, but not when it requires extra equipment. Another negative is that heating with air requires longer recharge times.
The Nuclear Engineering Department at MIT and the startup Rondo Energy popularized the idea of using resistors (toaster wire) integrated with bricks for heating. It is substantially cheaper than charging with hot air, unlocks faster charging, and allows continuous operation of the system.
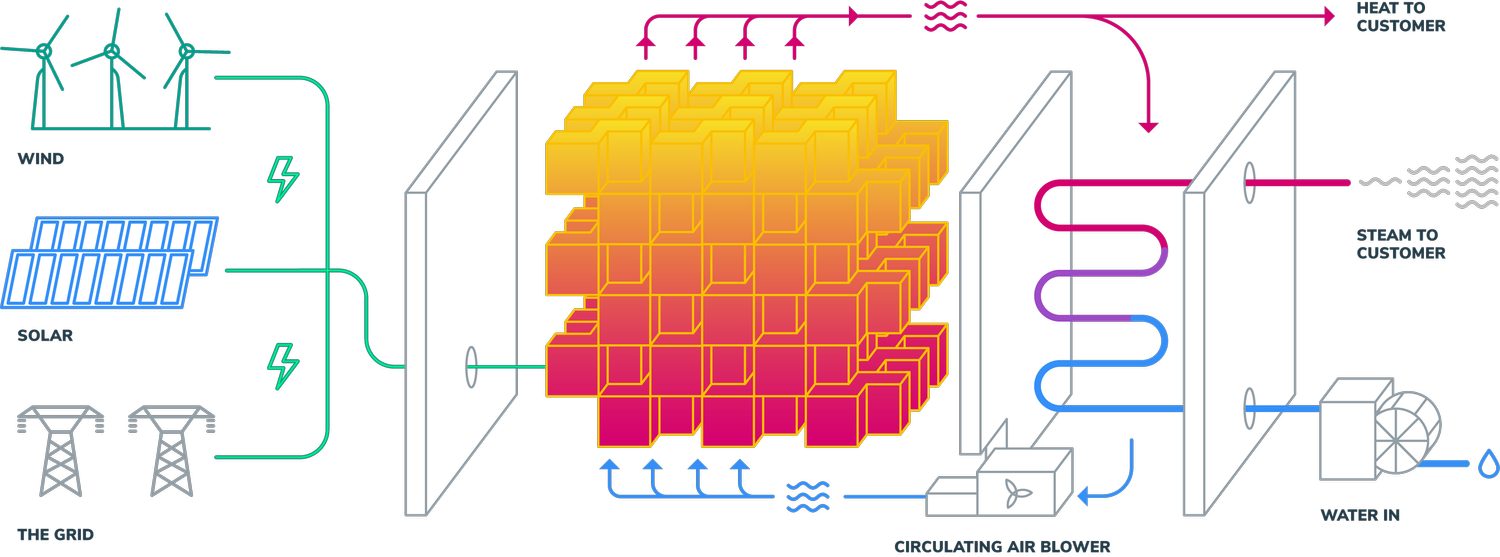
Source: Rondo.com
The downsides are that the brick form factors are slightly different, and the wire limits the maximum temperature to around 1500C. Customers aren't bothered. Rondo is building a 90 gigawatt hours/year factory to meet demand. Remarkably, a small startup founded in 2020 is setting up a larger facility than any existing lithium-ion battery factory, highlighting the scalability of bricks.
Upgrading to Conductive Bricks
One reason that competing startups choose graphite is that it conducts electricity. The thermal mass can also be the resistor, simplifying the design by removing air heaters and toaster wire. The ideal solution would be conductive bricks. Electrified Thermal Solutions, spun out of MIT Nuclear Engineering, is commercializing such a technology. They accomplish this by doping the bricks with elements that make them conductive.
Conductive bricks allow faster heating by eliminating the bottleneck of conduction between the wires and bricks. They also make it cheaper to increase charging power by integrating so much of the charging infrastructure. The bricks can also use the traditional form factor and layout, easing manufacturing. Most important is that the maximum temperature increases, opening up markets like cement and blast furnaces.
The downside is that the technology isn't as mature, there might be issues with brick longevity from the tiny dopants, and scaling is happening a year or two behind more conservative designs like Rondo Energy uses.
Applications
Steam
Steam delivers roughly half of industrial heat consumption. And most steam temperatures are below 400C. The process for making steam from hot bricks is to blow air through the bricks and then use the hot air to produce steam in a heat recovery boiler. Facilities like natural gas combined cycle power plants already use these boilers. The moderate temperatures and simple equipment make steam the obvious market entry point, especially in sunny regions closer to the equator.
The economics push towards on-site renewables in most cases. Grid electricity is usually expensive. Negative wholesale electricity prices stir excitement, but these prices are location-dependent and don't include transmission and delivery charges. Those charges often make up the majority of an electricity bill. Utilities fight hard to deny customers direct access to wholesale markets. And the equipment to handle grid electricity is expensive. A transformer can cost as much as the entire storage system, doubling the installed cost.
Hooking up solar panels directly to the storage system removes inverter and utility interconnection costs. Wind power could contribute in some instances, but most facilities won't have cost-effective wind resources nearby, and the turbine spacing requires a much larger footprint.
The specific project economics will determine how much fuel consumption the solar PV + brick system displaces. Models can predict yearly solar output with 1% accuracy, but day-to-day production matters for plant operation. Extra solar electricity in the summer doesn't help a factory meet winter production goals. Slightly overbuilding solar PV + brick capacity might provide 100% of steam production in locations with less seasonal variation. A facility at a higher latitude might continue to burn some fuel in the winter rather than add more solar panels with a high summer curtailment rate. Or they could sell excess solar through an existing grid connection and buy outside electricity in the winter. Low capacity factor expansions might be cheaper than buying fuel if solar prices continue to fall. It is common for plants to maintain multiple fuels for steam generation. They will use whatever is the cheapest.
Solar PV plus brick storage could be very cheap. A solar farm produces electricity that costs anywhere from $25-$40/MWh when connected to the grid. $20-$30/MWh for off-grid could be a reasonable assumption. That equals $5.75-$9/MCF of gas or $140-$210/ton of coal. Those prices are already cheaper than much of the world's energy prices at trading hubs. On-site electricity is more competitive than it appears because the efficiency of a thermal storage system is often higher than fossil fuel boilers, and delivery costs for fossil fuel add significantly to end-user costs.
The cycle cost of the brick storage is surprisingly low. One estimate for an off-grid brick and toaster wire setup is $5/kWh. Adding the steam generator doubles this cost. Daily cycling over a thirty-year life would imply an undiscounted cycle cost of $1/MWh. Discounting and some excess capacity would increase cycle cost to $1.50-$2.50/MWh. These systems would be competitive with fuel anywhere on Earth if off-grid solar prices fell to $10/MWh (except maybe a mine mouth or gas field).
I've written before that geothermal could be a strong competitor in the steam market. Geothermal is consistent throughout the year, making it more competitive at higher latitudes. A sweet spot is applications like district heating, where demand peaks in the winter. Solar PV + bricks are more modular and require significantly less human capital than drilling geothermal wells. It will be a race for market share.
Drying/Direct Heating
Drying and direct heating <1000C are applications with very similar characteristics to the steam market. The main difference is deleting the steam generator. Air can provide the heating, or the process fluid may travel through the bricks.
Blast Furnaces/Steel
Steel and cement production are relatively minor heat users in the US but loom large globally. Much of the steel production in the US already happens in electric arc furnaces. Cement and steel-hungry infrastructure isn't expanding at rapid rates. Developing countries have less steel scrap, use less wood in construction, and need massive amounts of new infrastructure, driving integrated steel and cement production.
Integrated steel production produces emissions through heating and using coking coal to reduce iron. Electricity-derived heat can roughly halve coal usage by increasing inlet air temperature to ~1900 C. The coal burned in the furnace nears the minimum needed to reduce iron.
Operating under these conditions adds several challenges. Our toaster wire can't get hot enough, and our bricks must be of higher quality. Conductive bricks could solve these issues. Hot air may not provide enough heat transfer. Gases like carbon dioxide might be necessary, which makes the system more complex than just blowing air. There will still be combustion, so the outlet gas steam will not be easy to capture pure CO2 and water unless the steel plant uses pure oxygen. You can theoretically modify existing furnaces for hotter inlet air, but there would need to be extensive testing to determine how reducing coal burn would impact steel quality.
The system also requires more storage to support high temperatures. The outlet is always 1900C, meaning some bricks must remain at that temperature. Those bricks can't release their full energy. The amount of extra storage required depends on the design. Air will rapidly reduce the brick temperature near the inlet because the temperature delta and driving force are highest. The air is hot before it reaches the outlet, and little heat will transfer. Bricks transfer less heat as they cool, and the next bricks in line handle more heat transfer. The airflow creates a temperature gradient that moves towards the outlet over time. Bricks near the outlet won't release as much energy as a system producing 300C steam.
An advantage that brick storage has for reducing coal in blast furnaces is that coking coal is much more expensive than thermal coal. It doesn't kill the business case if the cost per cycle increases. $15-$20/MWh solar may be enough to eliminate the portion of coking coal that provides heat at some mills.
Cement
Cement production has many of the same challenges as blast furnaces since it requires up to 1800C temperatures, needs rapid heat transfer, and any retrofit will impact the heart of the process. Cement kilns often use thermal coal, making cost competitiveness challenging.
Replacing the coal for heating will only reduce carbon dioxide emissions by ~35%-50%. It will eliminate combustion so that a pure carbon dioxide stream can exit the stack, reducing the capture cost. Carbon dioxide slows the calcination reaction, creating tradeoffs.
One feature of cement is that transportation is a significant portion of the customer's price. Using solar PV + bricks to eliminate energy transportation allows new plants to optimize location based on customers and raw material sourcing. And there are locations where it is difficult to permit a cement plant because of air pollution rules. Almost all of these locations are near cities (and customers). A new facility without air emissions from burning coal could move much closer to customers without needing extensive emissions scrubbers.
Other startups, including our toaster wire and bricks folks, are working on lower-temperature pathways to making cement. These efforts are still in the very early stages.
Solar PV + bricks won't sweep the cement industry overnight, but there could be substitution in regions with high energy prices. Conversion will be more widespread if off-grid solar falls below $10/MWh.
Repowering Fossil Fuel Power Plants
Multi-Day Storage
Many thermal power plant technologies struggle to compete against solar, wind, gas, and batteries because their steam turbines are expensive. Geothermal, fission, and fusion proponents have suggested "re-powering" retiring coal power plants. We've seen steam turbines reused before as utilities converted equipment from helium-cooled nuclear reactors and coal power plants to natural gas fuel. Thermal storage might throw its hat in, too.
It seems likely that efficient batteries will handle most hourly storage. Studies have shown that the next possible niche is multi-day storage, around 100 hours. Lower efficiency but cheap technologies can compete against low-utilization batteries, especially with more seasonal impacts and higher wind penetration. High-temperature brick storage beats a competing technology like iron-air batteries in cost, trounces it in recharge speed, and has slightly lower efficiency. But the real competitors are natural gas power plants. They can break even at $35-$50/MWh when fuel prices are under $4/MCF, even at 10%-20% utilization.
Our bricks will be more expensive for this job than industrial applications because they will have lower utilization. A system with 100+ hour cycles will have 1/4 the cycles to earn money from (or less!). Having extra cycles thirty years from now isn't worth much because of the time value of money. But value engineering can claw some of the cost increases back. Steam temperatures for a coal power plant are easy to meet because they are 500-700C. Lower-grade refractory bricks are much cheaper by mass and maybe half the cost per kWh due to lower storage temperature. Lower temperatures could also allow the use of less expensive wire. The blower and steam generator sizes are much smaller relative to the storage amount. Power plant applications tend to be larger than process heat, allowing economics of scale in equipment. Surface area falls relative to volume, reducing the cost of the container and insulation. A cycle might cost $10/MWh as a result.
Purchasing energy is the primary cost. The coal power plant turbines are 45%-50% efficient. The optimal amount of insulation for this duration results in 1%-2% daily heat loss. Overall efficiency will be around 40%. Buying electricity at $10-$15/MWh would require $35-$48/MWh to pay for energy and storage costs. The system can compete with existing gas power plants.
Very high-temperature systems might be able to re-power natural gas combined cycle power plants. The efficiency will be higher but offset by increased storage cost, resulting in similar breakeven prices. Combined heat and power systems are another possible target for fuel replacement. Technology like thermovoltaic panels may eventually allow new builds at competitive prices.
A new steam turbine might increase installed costs several times for a 100-hour storage project. Total costs would increase to $55-$70/MWh. Those prices are more expensive than existing gas power plants in the US but would be cheaper where natural gas costs more than ~$7/MCF. They would fare better against new builds but still struggle where capacity factors are as low as 10% unless fuel prices are high. Other technologies, like hot air-driven gas turbines or supercritical CO2 turbines, might be more affordable if electricity purchase costs or capacity factors are low. But there is no shortage of steam turbines in coal, oil, or combined cycle power plants. Average global electricity usage is ~2.5 TW. There are 2.2 TW of existing coal power plants alone.
The model for these systems would likely be turning existing power plants into renewables hubs. Solar and wind use the existing grid connection and charge batteries when there is excess production. Thermal storage takes any electricity the batteries can't absorb. The thermal storage powers the legacy power plant when there are shortfalls from renewables and batteries. In many regions, a modest amount of 100-hour storage may be enough to ditch 99% of fossil fuel electricity generation (Australia, Arizona, etc.).
Seasonal Storage
100-hour storage will only meet about half the shortfall someplace like New York. Seasonal storage is still a requirement unless solar and wind are overbuilt by 3x-5x. But seasonal storage is horrifically challenging because a system might only get 1-2 cycles per year. Chemical storage is the typical answer due to its high energy density. Our natural gas storage reservoirs earn one cycle per year. Natural gas is hard to beat, and many clean tech proponents assume we will ban it and use more expensive hydrogen instead. Others suggest synthetic fuel. Any prospective seasonal storage system requires capital expenditure of <$1/kWh to beat gas.
Our fancy brick systems are immediately out of the running, but a closer look at the requirements suggests some possibilities:
-
Running old coal power plants doesn't require 1500 C storage.
-
Cycles Are Limited
The lifetime cycles might be 30-50 instead of thousands. Lower temperatures and limited cycles open up materials like crushed granite or sand.
-
Seasonal storage doesn't require ramping
Our natural gas storage system charges slowly for eight months and then slowly drains in the winter. Any seasonal storage system can have extremely low power density. Other technologies, like batteries, will handle the day-to-day swings.
Charles Forsberg examines a thermal system with many of the characteristics we need. The idea is a big pile of crushed granite in a metal building. A 250m x 250m x 20m pile could hold 100 gigawatt hours of energy. The volume helps limit heat loss without requiring excessive insulation by decreasing the surface area-to-volume ratio. Lower temperature means lower-grade heating wires can work. However, the fluid choice adds significant cost because the proposal calls for molten salt or oil instead of air. The case against air is that the heat exchangers would be too costly, and the pressure drop would be too high. The hope is for a $2-$4/kWh system cost, well above the target for seasonal storage.
We can correct many of these issues if we lean into low power density. Forsberg's proposal calls for a 30-hour discharge. A seasonal system might take weeks or months to discharge. The heat exchanger to produce steam from hot air won't be a meaningful portion of the cost if the power-to-storage ratio is 25x-100x smaller. Charging CAPEX can be reasonable whether we use steel wires or hot air because the process will happen over 8-9 months. Discharge air velocity will be lower, lessening pressure drop. A system that discharges in 30 hours needs relatively tiny chunks of rock because heat conduction within the rock becomes limiting. Boulders are fine at lower power density, lowering pressure drop further.
It costs $0.15-$0.35/KWh for the storage material. Keeping overall costs reasonable relies on scale to decrease the cost of associated systems like insulation and low power density to limit charge and discharge capital. The hangar's purpose is to protect systems related to the oil or salt and shouldn't be necessary with air as a fluid. Using the granite pile to support the insulation could be cheaper. 120 days of storage for a 500 MW coal plant would require almost 3000 gigawatt hours or 500 acres of rock stacked 20 meters high. Moving the mass, site organization, and hot air/steam piping will be difficult! Making the piles taller and breaking them into subunits might be necessary. Specialized equipment could be a worthwhile investment to get rocks from railcars into piles. Big mining dump trucks that hold hundreds of tons cost surprisingly little, <$10 million. One Cat 797 running 24/7 could move enough rock for 3000 gigawatt hours of storage in a little over a year with the help of some loading and spreading equipment.
Anywhere from $0.30-$0.50/kWh could be possible. The cycle cost would be $40-$60/MWh of electricity at a 5% discount rate, one cycle per year, and a thirty-year life. The break-even price would be 2.5x the purchase price plus the cycle cost. That maps to $53/MWh-$63/MWh if the storage system bought summertime excess power for $5/MWh. A New York solar farm selling at those prices would get paid $10-$15/MWh on average over the year. Those costs may be too high in the US but would be competitive in much of the world.
There are many engineering challenges in scaling up a massive facility, and these optimistic costs may not work economically. But they do create a bound for what alternatives are practical. Natural gas would need to stay below ~$5/MCF. Hydrogen seasonal storage viability looks grim. The max average earnings for a baseload power plant would be in the neighborhood of $35/MWh if cheap batteries limited nighttime prices. That is near the operating cost of our current nuclear fleet. Transmission lines would need to be regional and have high utilization rates. We probably won't be transmitting wind power from Nebraska to Buffalo! It might be cheaper to overbuild local wind and solar, use more 100-hour systems, and size the seasonal storage system for 1-2 months of discharge to arbitrage prices better. Maybe another technology can figure out how to fuel the old power plants for less money. Markets are great at figuring these things out.
A new turbine for a seasonal project would increase the system capital expenditure by ~40%. That would increase the overall cost by ~25%, which is expensive but not debilitating. A 100-hour storage facility is buying electricity at everyday prices. It spends more on fuel and must economize on capital expenditure. A seasonal storage system at high latitude is moving nearly free summer surplus electricity to winter. It spends much less on buying "fuel" but more on capital expenditure.
A seasonal model like this might be relevant for high-latitude steam users.
There is no market for seasonal systems like this today, but perhaps there will be in high-latitude regions as solar costs continue to fall.
Finding the Space for Solar
Many of these applications require inexpensive solar near existing infrastructure. Solar has a reputation for needing excessive land. Improvement in panel efficiency and the emergence of ground-mounted solar systems mean land needs are roughly one-quarter of what they were 5-10 years ago. These same advancements also lower the cost. Solar might cost $10-$15/MWh without inverters or grid connections before 2026.
The Future of Solar PV + Bricks
Brick heat storage for process steam has compelling economics and minimal technical challenges. Design variations could proliferate rapidly to minimize the cost based on process temperature and seasonality.
Specialized applications like powering cement kilns and blast furnaces will require more extensive testing before substitution can happen.
Gatekeepers like grid operators or local planning departments constrain solar PV growth. Onsite power production at industrial facilities offers an opportunity for breakneck growth. It could be a perfect storm for countries with substantial solar incentives. The US Inflation Reduction Act solar subsidies are generous enough that a solar PV + brick system could cost $0 for an industrial buyer with taxable income. Developers tired of waiting in interconnection queues will go hunting for these customers.
Multi-day and seasonal energy storage could be surprisingly competitive when utilizing existing turbines. The low cost of thermal storage could thin out many competing technologies and provide solutions for high-latitude regions.
The highest-level takeaway is that thermal storage can flatten global energy prices. Industrial-strength energy will be available in every region at fossil fuel prices or lower. There is a limit to how much cost seasonal variation can add. Ubiquitous thermal storage makes the energy transition debate much more boring.
The Case for Brick Thermal Storage
2023 September 8 Twitter Substack See all postsThermal storage could solve many difficult areas of decarbonization.
The Appeal of Storing Heat (in Bricks)
Thermal Storage vs. Alternatives
Thermal storage is inexpensive and has moderate energy density but remains niche. Fossil fuels excel at producing heat, and storing that heat adds unnecessary cost. Oil contains ~40x more energy per unit mass than refractory bricks can store.
A handful of startups are taking a second look at thermal storage with the rise of variable renewables. It is ~50x cheaper per kilowatt hour than lithium-ion batteries. Any mass can store heat, often with minimal physical change. Electrochemical batteries are complex devices requiring pricey materials and elaborate manufacturing processes that increase cost. But batteries can efficiently store electricity while heat is expensive to convert back into electricity. Thermal storage can beat batteries by providing heat or operating for longer durations.
Industrial heat makes up 26% of global final energy usage, providing ample opportunity for thermal storage.
Pumped hydro storage and compressed air storage are other technologies deployed at scale. Both have abysmal energy density. Finding suitable locations is challenging. Thermal storage is ~100x more dense, on par with electrochemical batteries. It is compact enough to fit near factories and other users.
Thermal storage can be compelling when matching cheap electricity from renewables and users that require heat.
The Virtue of Bricks
The ideal heat storage material is a solid with a high melting point, doesn't fall apart with thermal cycling, has good heat capacity, and is cheap. The few liquids that can handle high temperatures have unpleasant properties. Solids can act as the heat exchange interface, lowering costs when heating gases. A higher melting point increases storage because the energy stored is the temperature delta multiplied by the heat capacity. Increasing the maximum temperature is necessary for applications like cement kilns. Many solids crumble under thermal stress, shortening system life, so materials must be stable.
Refractory bricks made of silicon dioxide and aluminum oxide are a classic solution. Competing materials like loose sand, crushed rock, or graphite have lower heat capacities, melting points, and densities. Graphite has further issues because it tends to oxidize at high temperatures. Mixtures like aluminum oxide and silicon dioxide in bricks store more energy in less space and mass while still being dirt cheap and stable.
The Evolution of Brick Heat Storage
Blast Furnaces and Cowper Stoves
A key advance in iron production was "hot blast," or preheated air. Hot inlet air allows the furnace temperature to increase and fuel consumption to decrease. Another advance was the Cowper Stove. They are giant heat regenerators that capture waste heat from the exhaust and use it to preheat fresh air to create the "hot blast."
The regenerators are usually a tower filled with bricks arranged in a checkerboard fashion. A blast furnace might use 3-4. Exhaust air flows through the bricks, heating them. The exhaust is switched to another regenerator once the bricks are hot. Operators blow fresh air through the hot bricks until they cool. A Cowper Stove-style regenerator usually goes through 24 cycles per day and has a service life of 30 years, thanks to many incremental improvements in brick manufacturing. The cumulative storage capacity of these systems is in the gigawatt hours.
Cowper Stove Source: Sciencedirect.com
The application favors brick towers over traditional heat exchangers for several reasons. High temperatures paired with acid gases make material selection a challenge for heat exchangers that are typically metal, but the bricks are very durable. Gas-gas heat exchangers can be enormous because gases have lower thermal conductivity. The checkered bricks provide extensive surface area for heat transfer. Heat exchangers are more efficient when fluid velocity is high, but this increases pressure drop. The brick towers have very low-pressure drop. Facilities can use inexpensive blowers in place of pricier compressors.
Brick heat storage improves blast furnaces and can operate in an environment that challenges traditional heat exchange methods. Hundreds (or thousands!) of years of brick technological development make them an asset for future thermal storage systems.
Heating Bricks With Toaster Wire
Early concepts for using bricks to store renewable electricity deviated from existing designs as little as possible. A blower would push air through an electric heater and past the bricks, making them hot. The system could run in reverse to recover the heat. The hot air would heat a process directly or produce steam in a boiler.
The challenge is that electric heaters for air are large and expensive. Heating the bricks with air makes sense when it is waste heat from a furnace, but not when it requires extra equipment. Another negative is that heating with air requires longer recharge times.
The Nuclear Engineering Department at MIT and the startup Rondo Energy popularized the idea of using resistors (toaster wire) integrated with bricks for heating. It is substantially cheaper than charging with hot air, unlocks faster charging, and allows continuous operation of the system.
Source: Rondo.com
The downsides are that the brick form factors are slightly different, and the wire limits the maximum temperature to around 1500C. Customers aren't bothered. Rondo is building a 90 gigawatt hours/year factory to meet demand. Remarkably, a small startup founded in 2020 is setting up a larger facility than any existing lithium-ion battery factory, highlighting the scalability of bricks.
Upgrading to Conductive Bricks
One reason that competing startups choose graphite is that it conducts electricity. The thermal mass can also be the resistor, simplifying the design by removing air heaters and toaster wire. The ideal solution would be conductive bricks. Electrified Thermal Solutions, spun out of MIT Nuclear Engineering, is commercializing such a technology. They accomplish this by doping the bricks with elements that make them conductive.
Conductive bricks allow faster heating by eliminating the bottleneck of conduction between the wires and bricks. They also make it cheaper to increase charging power by integrating so much of the charging infrastructure. The bricks can also use the traditional form factor and layout, easing manufacturing. Most important is that the maximum temperature increases, opening up markets like cement and blast furnaces.
The downside is that the technology isn't as mature, there might be issues with brick longevity from the tiny dopants, and scaling is happening a year or two behind more conservative designs like Rondo Energy uses.
Applications
Steam
Steam delivers roughly half of industrial heat consumption. And most steam temperatures are below 400C. The process for making steam from hot bricks is to blow air through the bricks and then use the hot air to produce steam in a heat recovery boiler. Facilities like natural gas combined cycle power plants already use these boilers. The moderate temperatures and simple equipment make steam the obvious market entry point, especially in sunny regions closer to the equator.
The economics push towards on-site renewables in most cases. Grid electricity is usually expensive. Negative wholesale electricity prices stir excitement, but these prices are location-dependent and don't include transmission and delivery charges. Those charges often make up the majority of an electricity bill. Utilities fight hard to deny customers direct access to wholesale markets. And the equipment to handle grid electricity is expensive. A transformer can cost as much as the entire storage system, doubling the installed cost.
Hooking up solar panels directly to the storage system removes inverter and utility interconnection costs. Wind power could contribute in some instances, but most facilities won't have cost-effective wind resources nearby, and the turbine spacing requires a much larger footprint.
The specific project economics will determine how much fuel consumption the solar PV + brick system displaces. Models can predict yearly solar output with 1% accuracy, but day-to-day production matters for plant operation. Extra solar electricity in the summer doesn't help a factory meet winter production goals. Slightly overbuilding solar PV + brick capacity might provide 100% of steam production in locations with less seasonal variation. A facility at a higher latitude might continue to burn some fuel in the winter rather than add more solar panels with a high summer curtailment rate. Or they could sell excess solar through an existing grid connection and buy outside electricity in the winter. Low capacity factor expansions might be cheaper than buying fuel if solar prices continue to fall. It is common for plants to maintain multiple fuels for steam generation. They will use whatever is the cheapest.
Solar PV plus brick storage could be very cheap. A solar farm produces electricity that costs anywhere from $25-$40/MWh when connected to the grid. $20-$30/MWh for off-grid could be a reasonable assumption. That equals $5.75-$9/MCF of gas or $140-$210/ton of coal. Those prices are already cheaper than much of the world's energy prices at trading hubs. On-site electricity is more competitive than it appears because the efficiency of a thermal storage system is often higher than fossil fuel boilers, and delivery costs for fossil fuel add significantly to end-user costs.
The cycle cost of the brick storage is surprisingly low. One estimate for an off-grid brick and toaster wire setup is $5/kWh. Adding the steam generator doubles this cost. Daily cycling over a thirty-year life would imply an undiscounted cycle cost of $1/MWh. Discounting and some excess capacity would increase cycle cost to $1.50-$2.50/MWh. These systems would be competitive with fuel anywhere on Earth if off-grid solar prices fell to $10/MWh (except maybe a mine mouth or gas field).
I've written before that geothermal could be a strong competitor in the steam market. Geothermal is consistent throughout the year, making it more competitive at higher latitudes. A sweet spot is applications like district heating, where demand peaks in the winter. Solar PV + bricks are more modular and require significantly less human capital than drilling geothermal wells. It will be a race for market share.
Drying/Direct Heating
Drying and direct heating <1000C are applications with very similar characteristics to the steam market. The main difference is deleting the steam generator. Air can provide the heating, or the process fluid may travel through the bricks.
Blast Furnaces/Steel
Steel and cement production are relatively minor heat users in the US but loom large globally. Much of the steel production in the US already happens in electric arc furnaces. Cement and steel-hungry infrastructure isn't expanding at rapid rates. Developing countries have less steel scrap, use less wood in construction, and need massive amounts of new infrastructure, driving integrated steel and cement production.
Integrated steel production produces emissions through heating and using coking coal to reduce iron. Electricity-derived heat can roughly halve coal usage by increasing inlet air temperature to ~1900 C. The coal burned in the furnace nears the minimum needed to reduce iron.
Operating under these conditions adds several challenges. Our toaster wire can't get hot enough, and our bricks must be of higher quality. Conductive bricks could solve these issues. Hot air may not provide enough heat transfer. Gases like carbon dioxide might be necessary, which makes the system more complex than just blowing air. There will still be combustion, so the outlet gas steam will not be easy to capture pure CO2 and water unless the steel plant uses pure oxygen. You can theoretically modify existing furnaces for hotter inlet air, but there would need to be extensive testing to determine how reducing coal burn would impact steel quality.
The system also requires more storage to support high temperatures. The outlet is always 1900C, meaning some bricks must remain at that temperature. Those bricks can't release their full energy. The amount of extra storage required depends on the design. Air will rapidly reduce the brick temperature near the inlet because the temperature delta and driving force are highest. The air is hot before it reaches the outlet, and little heat will transfer. Bricks transfer less heat as they cool, and the next bricks in line handle more heat transfer. The airflow creates a temperature gradient that moves towards the outlet over time. Bricks near the outlet won't release as much energy as a system producing 300C steam.
An advantage that brick storage has for reducing coal in blast furnaces is that coking coal is much more expensive than thermal coal. It doesn't kill the business case if the cost per cycle increases. $15-$20/MWh solar may be enough to eliminate the portion of coking coal that provides heat at some mills.
Cement
Cement production has many of the same challenges as blast furnaces since it requires up to 1800C temperatures, needs rapid heat transfer, and any retrofit will impact the heart of the process. Cement kilns often use thermal coal, making cost competitiveness challenging.
Replacing the coal for heating will only reduce carbon dioxide emissions by ~35%-50%. It will eliminate combustion so that a pure carbon dioxide stream can exit the stack, reducing the capture cost. Carbon dioxide slows the calcination reaction, creating tradeoffs.
One feature of cement is that transportation is a significant portion of the customer's price. Using solar PV + bricks to eliminate energy transportation allows new plants to optimize location based on customers and raw material sourcing. And there are locations where it is difficult to permit a cement plant because of air pollution rules. Almost all of these locations are near cities (and customers). A new facility without air emissions from burning coal could move much closer to customers without needing extensive emissions scrubbers.
Other startups, including our toaster wire and bricks folks, are working on lower-temperature pathways to making cement. These efforts are still in the very early stages.
Solar PV + bricks won't sweep the cement industry overnight, but there could be substitution in regions with high energy prices. Conversion will be more widespread if off-grid solar falls below $10/MWh.
Repowering Fossil Fuel Power Plants
Multi-Day Storage
Many thermal power plant technologies struggle to compete against solar, wind, gas, and batteries because their steam turbines are expensive. Geothermal, fission, and fusion proponents have suggested "re-powering" retiring coal power plants. We've seen steam turbines reused before as utilities converted equipment from helium-cooled nuclear reactors and coal power plants to natural gas fuel. Thermal storage might throw its hat in, too.
It seems likely that efficient batteries will handle most hourly storage. Studies have shown that the next possible niche is multi-day storage, around 100 hours. Lower efficiency but cheap technologies can compete against low-utilization batteries, especially with more seasonal impacts and higher wind penetration. High-temperature brick storage beats a competing technology like iron-air batteries in cost, trounces it in recharge speed, and has slightly lower efficiency. But the real competitors are natural gas power plants. They can break even at $35-$50/MWh when fuel prices are under $4/MCF, even at 10%-20% utilization.
Our bricks will be more expensive for this job than industrial applications because they will have lower utilization. A system with 100+ hour cycles will have 1/4 the cycles to earn money from (or less!). Having extra cycles thirty years from now isn't worth much because of the time value of money. But value engineering can claw some of the cost increases back. Steam temperatures for a coal power plant are easy to meet because they are 500-700C. Lower-grade refractory bricks are much cheaper by mass and maybe half the cost per kWh due to lower storage temperature. Lower temperatures could also allow the use of less expensive wire. The blower and steam generator sizes are much smaller relative to the storage amount. Power plant applications tend to be larger than process heat, allowing economics of scale in equipment. Surface area falls relative to volume, reducing the cost of the container and insulation. A cycle might cost $10/MWh as a result.
Purchasing energy is the primary cost. The coal power plant turbines are 45%-50% efficient. The optimal amount of insulation for this duration results in 1%-2% daily heat loss. Overall efficiency will be around 40%. Buying electricity at $10-$15/MWh would require $35-$48/MWh to pay for energy and storage costs. The system can compete with existing gas power plants.
Very high-temperature systems might be able to re-power natural gas combined cycle power plants. The efficiency will be higher but offset by increased storage cost, resulting in similar breakeven prices. Combined heat and power systems are another possible target for fuel replacement. Technology like thermovoltaic panels may eventually allow new builds at competitive prices.
A new steam turbine might increase installed costs several times for a 100-hour storage project. Total costs would increase to $55-$70/MWh. Those prices are more expensive than existing gas power plants in the US but would be cheaper where natural gas costs more than ~$7/MCF. They would fare better against new builds but still struggle where capacity factors are as low as 10% unless fuel prices are high. Other technologies, like hot air-driven gas turbines or supercritical CO2 turbines, might be more affordable if electricity purchase costs or capacity factors are low. But there is no shortage of steam turbines in coal, oil, or combined cycle power plants. Average global electricity usage is ~2.5 TW. There are 2.2 TW of existing coal power plants alone.
The model for these systems would likely be turning existing power plants into renewables hubs. Solar and wind use the existing grid connection and charge batteries when there is excess production. Thermal storage takes any electricity the batteries can't absorb. The thermal storage powers the legacy power plant when there are shortfalls from renewables and batteries. In many regions, a modest amount of 100-hour storage may be enough to ditch 99% of fossil fuel electricity generation (Australia, Arizona, etc.).
Seasonal Storage
100-hour storage will only meet about half the shortfall someplace like New York. Seasonal storage is still a requirement unless solar and wind are overbuilt by 3x-5x. But seasonal storage is horrifically challenging because a system might only get 1-2 cycles per year. Chemical storage is the typical answer due to its high energy density. Our natural gas storage reservoirs earn one cycle per year. Natural gas is hard to beat, and many clean tech proponents assume we will ban it and use more expensive hydrogen instead. Others suggest synthetic fuel. Any prospective seasonal storage system requires capital expenditure of <$1/kWh to beat gas.
Our fancy brick systems are immediately out of the running, but a closer look at the requirements suggests some possibilities:
Running old coal power plants doesn't require 1500 C storage.
Cycles Are Limited
The lifetime cycles might be 30-50 instead of thousands. Lower temperatures and limited cycles open up materials like crushed granite or sand.
Seasonal storage doesn't require ramping
Our natural gas storage system charges slowly for eight months and then slowly drains in the winter. Any seasonal storage system can have extremely low power density. Other technologies, like batteries, will handle the day-to-day swings.
Charles Forsberg examines a thermal system with many of the characteristics we need. The idea is a big pile of crushed granite in a metal building. A 250m x 250m x 20m pile could hold 100 gigawatt hours of energy. The volume helps limit heat loss without requiring excessive insulation by decreasing the surface area-to-volume ratio. Lower temperature means lower-grade heating wires can work. However, the fluid choice adds significant cost because the proposal calls for molten salt or oil instead of air. The case against air is that the heat exchangers would be too costly, and the pressure drop would be too high. The hope is for a $2-$4/kWh system cost, well above the target for seasonal storage.
We can correct many of these issues if we lean into low power density. Forsberg's proposal calls for a 30-hour discharge. A seasonal system might take weeks or months to discharge. The heat exchanger to produce steam from hot air won't be a meaningful portion of the cost if the power-to-storage ratio is 25x-100x smaller. Charging CAPEX can be reasonable whether we use steel wires or hot air because the process will happen over 8-9 months. Discharge air velocity will be lower, lessening pressure drop. A system that discharges in 30 hours needs relatively tiny chunks of rock because heat conduction within the rock becomes limiting. Boulders are fine at lower power density, lowering pressure drop further.
It costs $0.15-$0.35/KWh for the storage material. Keeping overall costs reasonable relies on scale to decrease the cost of associated systems like insulation and low power density to limit charge and discharge capital. The hangar's purpose is to protect systems related to the oil or salt and shouldn't be necessary with air as a fluid. Using the granite pile to support the insulation could be cheaper. 120 days of storage for a 500 MW coal plant would require almost 3000 gigawatt hours or 500 acres of rock stacked 20 meters high. Moving the mass, site organization, and hot air/steam piping will be difficult! Making the piles taller and breaking them into subunits might be necessary. Specialized equipment could be a worthwhile investment to get rocks from railcars into piles. Big mining dump trucks that hold hundreds of tons cost surprisingly little, <$10 million. One Cat 797 running 24/7 could move enough rock for 3000 gigawatt hours of storage in a little over a year with the help of some loading and spreading equipment.
Anywhere from $0.30-$0.50/kWh could be possible. The cycle cost would be $40-$60/MWh of electricity at a 5% discount rate, one cycle per year, and a thirty-year life. The break-even price would be 2.5x the purchase price plus the cycle cost. That maps to $53/MWh-$63/MWh if the storage system bought summertime excess power for $5/MWh. A New York solar farm selling at those prices would get paid $10-$15/MWh on average over the year. Those costs may be too high in the US but would be competitive in much of the world.
There are many engineering challenges in scaling up a massive facility, and these optimistic costs may not work economically. But they do create a bound for what alternatives are practical. Natural gas would need to stay below ~$5/MCF. Hydrogen seasonal storage viability looks grim. The max average earnings for a baseload power plant would be in the neighborhood of $35/MWh if cheap batteries limited nighttime prices. That is near the operating cost of our current nuclear fleet. Transmission lines would need to be regional and have high utilization rates. We probably won't be transmitting wind power from Nebraska to Buffalo! It might be cheaper to overbuild local wind and solar, use more 100-hour systems, and size the seasonal storage system for 1-2 months of discharge to arbitrage prices better. Maybe another technology can figure out how to fuel the old power plants for less money. Markets are great at figuring these things out.
A new turbine for a seasonal project would increase the system capital expenditure by ~40%. That would increase the overall cost by ~25%, which is expensive but not debilitating. A 100-hour storage facility is buying electricity at everyday prices. It spends more on fuel and must economize on capital expenditure. A seasonal storage system at high latitude is moving nearly free summer surplus electricity to winter. It spends much less on buying "fuel" but more on capital expenditure.
A seasonal model like this might be relevant for high-latitude steam users.
There is no market for seasonal systems like this today, but perhaps there will be in high-latitude regions as solar costs continue to fall.
Finding the Space for Solar
Many of these applications require inexpensive solar near existing infrastructure. Solar has a reputation for needing excessive land. Improvement in panel efficiency and the emergence of ground-mounted solar systems mean land needs are roughly one-quarter of what they were 5-10 years ago. These same advancements also lower the cost. Solar might cost $10-$15/MWh without inverters or grid connections before 2026.
The Future of Solar PV + Bricks
Brick heat storage for process steam has compelling economics and minimal technical challenges. Design variations could proliferate rapidly to minimize the cost based on process temperature and seasonality.
Specialized applications like powering cement kilns and blast furnaces will require more extensive testing before substitution can happen.
Gatekeepers like grid operators or local planning departments constrain solar PV growth. Onsite power production at industrial facilities offers an opportunity for breakneck growth. It could be a perfect storm for countries with substantial solar incentives. The US Inflation Reduction Act solar subsidies are generous enough that a solar PV + brick system could cost $0 for an industrial buyer with taxable income. Developers tired of waiting in interconnection queues will go hunting for these customers.
Multi-day and seasonal energy storage could be surprisingly competitive when utilizing existing turbines. The low cost of thermal storage could thin out many competing technologies and provide solutions for high-latitude regions.
The highest-level takeaway is that thermal storage can flatten global energy prices. Industrial-strength energy will be available in every region at fossil fuel prices or lower. There is a limit to how much cost seasonal variation can add. Ubiquitous thermal storage makes the energy transition debate much more boring.