The Problem
Construction productivity is a topic that has interested me for years. When an engineer sees an inefficient process with no improvement, it ticks them off. Construction is error-prone, expensive, and suffers delays. The government thinks construction productivity has slightly decreased since 1960. It just needs some clever engineering and solutions, but which ones? This post will focus on the ubiquitous single-family home.
Why Things Aren't Getting Better
Here is the one-liner:
The combination of consumer tastes, low dollar value per volume building components, and the complexity of buildings inhibit efforts to scale.
Let's break that down.
Economics of Moving Bulky Items
Whether you are shipping 100 boxes of cellulose insulation or 100 boxes of computer chips, transportation from place A to place B costs about the same. As a percentage of what the product is worth, the transportation cost is vastly different. Computer chips are so valuable that the transportation will be a rounding error. The cost of transporting the insulation can be more than what it cost to manufacture the insulation.
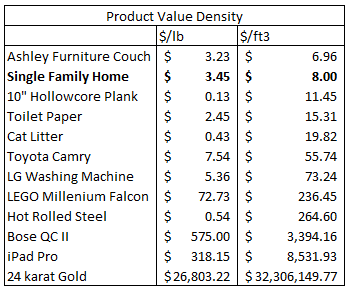
Source: constructionphysics.substack.com
Manufacturing for industries like computer chips happens in a few enormous factories. Manufacturing for low value per weight products like building materials happens in hundreds or thousands of small factories close to building sites to reduce transportation costs.
High volume, centralized manufacturing is one of the fastest ways to reduce costs. Think of the products that crash in price: CPUs, solar panels, lithium-ion batteries, flat-panel TVs. The most talented people run a few giant factories and can afford to invest in almost every conceivable process improvement. Manufacturing things like cement, insulation, or 2x4s means you have the assistant branch manager and a few hourly workers toiling in a glorified warehouse. At small factories, improvements often do not make sense. Even if they do, they are challenging to implement at all facilities.
This reality challenges new ideas for building fabrication.
Efforts to Scale and Standardize
"Let's build buildings like cars!" is the theme of most new building systems that get promoted. Cars are built very efficiently with high quality. They get better over time. Notice above that a Toyota Camry is roughly 7x more valuable per cubic foot than a house.
There are hundreds or possibly thousands of "prefab" ideas that have failed or failed to gain significant market share. The most popular variations are panels made offsite and assembled on the building site, modular sections that connect, or houses that unfold. Because of transportation costs, they are all limited to selling within a few hundred miles of their factory. Failure tends to happen when the market for housing declines. Companies are stuck with overhead from their factory, and transportation costs eat any cost advantage.
One successful example of prefab is trailer homes. New construction in the US is a little over $100 per square foot. Trailers cost $50-$60 per square foot. Cost savings come from cheap finishes and labor savings from manufacturing, while transportation costs are higher. Manufacturing plants are spread across the country to reduce transportation. This limits scale, so the process inside the factory is similar to a site-built home. It is not a factory full of robots. A factory might only build three homes a week. Models that have upgraded finishes are comparable in cost to new construction after site costs. The transportation cancels the factory efficiency gains. Trailers are a product that benefits many consumers but not a revolution in building construction.
Precast concrete panels are another small success story. Post-WWII, Eastern European countries built apartment buildings using this technology. Today, parking garages use precast concrete panels. Many poorer countries also have some adoption for housing construction. For precast panels to have a cost advantage, they need to be simple. It turns out most people do not want to live in communist-style apartment blocks. These panels are expensive to ship, so the market surrounding a factory is rarely large enough to support a large variety of designs.
Post-WWII suburbs may be the best example of mass-produced housing, Levittown being the most famous example. The demand for houses was incredible. Builders turned subdivisions into factories that produced thousands of homes. Each house was virtually identical, allowing clear divisions of labor and investment in things like sawmills to precut lumber. Each worker had a specific job, like "White Paint Man." A site might turn out dozens of houses per day. Builders built houses in under 90 days. The cost was reduced 20-30% to comparable models, with savings partially offset by capital costs for things like the sawmills. These methods never made up a majority of new home construction. They fell out of favor as consumers demanded more variation in housing, causing the economies of scale to disappear.
Construction Physics has a dizzying number of examples with all the details.
Consumer Tastes Drastically Increase Costs
People are obsessed with houses. Houses are a part of identity and status. There is near-universal derision for housing that is uniform and cookie cutter.
The construction industry already struggles to gain economies of scale because of transportation costs. Adding demand for uniqueness removes scale except at small level components like a 2x4.
Better-off consumers determine the features of new construction. Vinyl flooring, vinyl siding, one-piece shower stalls, and laminate countertops are examples of innovations that reduce the cost and increase durability. But most new houses have wood or tile floors, wood or brick siding, tile showers, and granite countertops because that is what sells. These buyers sometimes use their influence to codify these preferences into local zoning or building codes, making construction more expensive for anyone with cheaper taste.
Builders have responded by orienting their business around methods optimized to reduce overhead, tolerate errors, and allow variation in home design for the least cost possible.
Stick Frame Construction is Better Than You Think
Stick frame construction, also known as light-frame construction, was invented sometime in the 1830s. It did not take off until decades after. The industrial revolution allowed steam-powered sawmills and factories to lower the cost of 2x4s and nails. It grew into dominance over a few more decades.
It only looks inefficient. The method allows walls to support the structure and uses one-third the lumber that a comparable post-and-beam house does. Stick frame requires minimal skill to construct and is fast. Workers use only nail guns and saws. It is simple to integrate electrical, plumbing, and HVAC into stick-framed homes compared to other building systems. Framing supports any design. Site modifications are inexpensive if there are errors. Offsite building systems often suffer difficulty if things don't match up exactly right.
Some of the main disadvantages include difficulty in modeling due to inconsistency of the lumber and design complexity. Computer-aided design, modern sawmills, and selective breeding of trees are all working to improve these areas.
In a possible case study, note the productivity of multi-family construction. The first example of a "1+5" stick framed apartment building was in 1996. Building codes have become more friendly to this type of construction. "1+5s" are those 4-5 story rectangular apartment complexes that all look the same, popping up all over growing cities across the US.
Source: bls.gov
There are No Silver Bullets
No cost dominates the cost of new home construction. It is all nickels and dimes:
Source: constructionphysics.substack.com
Framing (green) is the highest cost but far from dominant at 15% of the total. Roughly 50% of the total cost is visible to the consumer - where taste matters. Reducing the cost means finding savings across a wide range of interconnected subsystems and still selling the house.
Improvement Requires Dumbing it Down and Raising our Ambitions
Almost every advancement in construction is small enough for a man to carry: 2x4s, nails, power tools, standard 4'x8' OSB sheathing, 4'x8' drywall, ZIP Sheathing, PEX piping. Each advancement fits within a simple construction system. Any complex attempt at prefab or modular, including by Toyota itself, has failed to reach any significant market share.
Reorganizing Construction is a Hard Way to Win
Prefabbing construction is almost always more expensive than comparable site-built construction. High overhead, capital intensity, and high transportation costs eat away at cost savings. Adoption rates of new technologies are painfully slow. On-site integration can be challenging.
I don't think it is impossible, but the execution has to be almost perfect. Even successes often end up as niche producers arbitraging regulations or labor costs.
General Purpose Technologies (GPTs) Rule
Flexible technologies that work within the current system and simplify processes have had the most success. These technologies allow the high precision and efficiency of factories to make it to the building site. The successful products are small and flexible. Small means they are cheaper to transport or pack efficiently. Flexibility means they can be used over and over on building sites. Adoption drives volumes large enough to justify moving from site-built to factory-built.
Here are some examples:
-
Experienced carpenters use chisels to create post and beam members on site. -> 2x4s and nails are mass manufactured and assembled by semi-skilled workers on site.
-
Workers assemble framing with hand saws and hammers. -> Workers use power saws, drills, and pneumatic nail guns to construct framing.
-
Workers measure individual boards and cut to sheath the framing. -> Workers nail manufactured 4'x8' OSB panels to frame as sheathing and subfloor.
-
Plumbers measure, cut, and sweat in each piece of copper pipe. -> PEX is unrolled, cut, and pulled into place.
-
Tyvek house wrap is stapled to OSB sheathing (and often damaged by wind) -> Water barrier is applied to OSB panels in a factory to make ZIP sheathing, reducing site work to taping seams.
-
Interior walls made of strips of wood and covered in plaster -> Interior walls made of 4'x8' sheets of drywall.
-
Window frames built on-site and glass installed -> Drop-in modular windows.
Where to Invest
Let's look at where the labor content is. Our ideas have to be able to survive decades-long adoption cycles. The dumber, the better.
Source: constructionphysics.substack.com
The best opportunity is in rough carpentry (framing) labor. I'll give one possible example, a combination of three technologies.
-
Some companies now precut lumber with a CNC-type machine according to construction drawings. Each piece gets stamped with directions on where it is supposed to go. Currently, workers are constantly measuring, sawing, and using the nail gun. Precut framing means only using the nail gun. The biggest challenge with this is the instructions sent to the cutter have to be correct, or on-site corrections eat efficiency gains. Precut framing is a new twist on an old idea. Sears kit homes consisted of precut framing, but the variation in design was limited. Digitizing the process allows one cutting plant to serve any light wood framing project.
-
Plans are only partially digitized. Quality of plans and what software engineers refer to as "version control" are not well executed. The software will likely improve over time through trial and error and continued adoption of standards that allow drawings to be interoperable. Any desire to tighten building tolerances and remove "site interpretation" will require better plans.
-
Most stick-framed designs are over-engineered to compensate for construction defects or poor-quality lumber. "Advanced Framing" is a set of design prescriptions that use better engineering models to reduce the use of wood in framing. Advanced framing also considers electrical, plumbing, and HVAC runs and organizes framing design to reduce installation time. Adoption is low for fear of lowering the safety factor in framing and the need for early coordination with other services. Better plans and precut and labeled lumber could decrease variation in construction, making adoption easier.
These technologies impact $18 per square foot of labor costs and $8 per square foot of material costs.
More ambitious technologies might create more gains:
-
Invent an extremely high R-value insulation and incorporate it into the sheathing, similar to ZIP-R, which uses foam. Remove the need for interior insulation. Removes $1 in labor plus removes coordination needs between insulation installer, plumbers, and electricians.
-
Drywall replacement that is a light panel and already pigmented with paint. Bonus points for the ability to be cured on-site to remove seams without taping, mudding, and sanding. Impact: $6.50 per square foot in labor costs, eliminate painting, increased flexibility, and time savings from reducing steps.
-
Modular electric wiring that is plug-and-play instead of manually installing Romex. Better yet, build nuclear batteries into every appliance and eliminate all wiring. Impact: $4 square foot, reduce steps and complexity.
-
Reduce plumbing costs by inventing a PEX version of sewer pipes. Flexible and unrolls to reduce installation labor. Replace gas appliances with electric or nuclear versions, eliminate gas piping. Impact: $5 per square foot.
-
Use the nuclear batteries and improved insulation to move to resistance heating and thermoelectric cooling. Use heat recovery ventilators (HRVs) for air circulation. Eliminate ducting. Impact: $3.50 per square foot and reducing coordination needs.
-
Roofing and foundations are areas that still need addressing through lighter, cheaper materials.
Full implementation might have cost reductions of 20%-30%. Substantial savings, but not transformational. Houses are complex, with many subsystems that are hard to replace or eliminate. We would need hundreds more ideas like these to get more substantial savings. Getting to a 50% reduction without cheapening finishes would be challenging. A "10x" reduction opportunity requires something like self-assembling nanotech structures. Any savings would likely get rolled into fancier countertops, floors, and fixtures.
Transformational cost reduction would have to come from changing what we think a house is. Imagine you had a thin suit that provided heating, cooling, processed your urine and waste, and kept you clean. Then you could have a house without bathrooms, insulation, heating, cooling, plumbing, and have the electrical eliminated with nuclear batteries. No kitchen because robotic takeout is so cheap. The house could cost $20 per square foot (with low-end finishes) and be smaller. A new home would go up in weeks. The technology is in the bodysuit instead of the house. Bodysuits can be mass-produced and shipped long distances. Ripe for cost reduction. The volumetric value of a home would be even lower.
The Easy Way to Unlock More Low-Cost Housing
How can we provide lower-cost housing today?
-
Trailers, duplexes, triplexes, or larger multi-family all use stick frame construction. Investment in stick framing compatible GPTs will positively impact these projects.
-
Trailers already cater to cost-conscious consumers. They are cheap at $50 per square foot. Eliminate the zoning regulations that restrict new trailer parks. Allow buyers to finance trailers as regular real estate. If the government subsidizes 30-year mortgages for well-off buyers, extend the same to trailer buyers. Better yet, remove all that involvement and level the playing field. If trailer sales increased, factories could be more numerous and closer to markets or increase volume, lowering costs.
-
Rezone to allow more multi-family construction and remove minimum parking requirements. America has some of the cheapest multi-family in the world. We need more of it!
If you think a new building system solves cost or availability, consider how it handles the value density problem and consumer tastes issues.
So, You Want to Build a House More Efficiently
2021 June 25 Twitter Substack See all postsThanks to Brian Potter's awesome blog, Construction Physics, for providing numbers and clarity to these ideas that would be murky otherwise. And thanks to many tech conversations with Eli Dourado.
The Problem
Construction productivity is a topic that has interested me for years. When an engineer sees an inefficient process with no improvement, it ticks them off. Construction is error-prone, expensive, and suffers delays. The government thinks construction productivity has slightly decreased since 1960. It just needs some clever engineering and solutions, but which ones? This post will focus on the ubiquitous single-family home.
Why Things Aren't Getting Better
Here is the one-liner:
The combination of consumer tastes, low dollar value per volume building components, and the complexity of buildings inhibit efforts to scale.
Let's break that down.
Economics of Moving Bulky Items
Whether you are shipping 100 boxes of cellulose insulation or 100 boxes of computer chips, transportation from place A to place B costs about the same. As a percentage of what the product is worth, the transportation cost is vastly different. Computer chips are so valuable that the transportation will be a rounding error. The cost of transporting the insulation can be more than what it cost to manufacture the insulation.
Source: constructionphysics.substack.com
Manufacturing for industries like computer chips happens in a few enormous factories. Manufacturing for low value per weight products like building materials happens in hundreds or thousands of small factories close to building sites to reduce transportation costs.
High volume, centralized manufacturing is one of the fastest ways to reduce costs. Think of the products that crash in price: CPUs, solar panels, lithium-ion batteries, flat-panel TVs. The most talented people run a few giant factories and can afford to invest in almost every conceivable process improvement. Manufacturing things like cement, insulation, or 2x4s means you have the assistant branch manager and a few hourly workers toiling in a glorified warehouse. At small factories, improvements often do not make sense. Even if they do, they are challenging to implement at all facilities.
This reality challenges new ideas for building fabrication.
Efforts to Scale and Standardize
"Let's build buildings like cars!" is the theme of most new building systems that get promoted. Cars are built very efficiently with high quality. They get better over time. Notice above that a Toyota Camry is roughly 7x more valuable per cubic foot than a house.
There are hundreds or possibly thousands of "prefab" ideas that have failed or failed to gain significant market share. The most popular variations are panels made offsite and assembled on the building site, modular sections that connect, or houses that unfold. Because of transportation costs, they are all limited to selling within a few hundred miles of their factory. Failure tends to happen when the market for housing declines. Companies are stuck with overhead from their factory, and transportation costs eat any cost advantage.
One successful example of prefab is trailer homes. New construction in the US is a little over $100 per square foot. Trailers cost $50-$60 per square foot. Cost savings come from cheap finishes and labor savings from manufacturing, while transportation costs are higher. Manufacturing plants are spread across the country to reduce transportation. This limits scale, so the process inside the factory is similar to a site-built home. It is not a factory full of robots. A factory might only build three homes a week. Models that have upgraded finishes are comparable in cost to new construction after site costs. The transportation cancels the factory efficiency gains. Trailers are a product that benefits many consumers but not a revolution in building construction.
Precast concrete panels are another small success story. Post-WWII, Eastern European countries built apartment buildings using this technology. Today, parking garages use precast concrete panels. Many poorer countries also have some adoption for housing construction. For precast panels to have a cost advantage, they need to be simple. It turns out most people do not want to live in communist-style apartment blocks. These panels are expensive to ship, so the market surrounding a factory is rarely large enough to support a large variety of designs.
Post-WWII suburbs may be the best example of mass-produced housing, Levittown being the most famous example. The demand for houses was incredible. Builders turned subdivisions into factories that produced thousands of homes. Each house was virtually identical, allowing clear divisions of labor and investment in things like sawmills to precut lumber. Each worker had a specific job, like "White Paint Man." A site might turn out dozens of houses per day. Builders built houses in under 90 days. The cost was reduced 20-30% to comparable models, with savings partially offset by capital costs for things like the sawmills. These methods never made up a majority of new home construction. They fell out of favor as consumers demanded more variation in housing, causing the economies of scale to disappear.
Construction Physics has a dizzying number of examples with all the details.
Consumer Tastes Drastically Increase Costs
People are obsessed with houses. Houses are a part of identity and status. There is near-universal derision for housing that is uniform and cookie cutter.
The construction industry already struggles to gain economies of scale because of transportation costs. Adding demand for uniqueness removes scale except at small level components like a 2x4.
Better-off consumers determine the features of new construction. Vinyl flooring, vinyl siding, one-piece shower stalls, and laminate countertops are examples of innovations that reduce the cost and increase durability. But most new houses have wood or tile floors, wood or brick siding, tile showers, and granite countertops because that is what sells. These buyers sometimes use their influence to codify these preferences into local zoning or building codes, making construction more expensive for anyone with cheaper taste.
Builders have responded by orienting their business around methods optimized to reduce overhead, tolerate errors, and allow variation in home design for the least cost possible.
Stick Frame Construction is Better Than You Think
Stick frame construction, also known as light-frame construction, was invented sometime in the 1830s. It did not take off until decades after. The industrial revolution allowed steam-powered sawmills and factories to lower the cost of 2x4s and nails. It grew into dominance over a few more decades.
It only looks inefficient. The method allows walls to support the structure and uses one-third the lumber that a comparable post-and-beam house does. Stick frame requires minimal skill to construct and is fast. Workers use only nail guns and saws. It is simple to integrate electrical, plumbing, and HVAC into stick-framed homes compared to other building systems. Framing supports any design. Site modifications are inexpensive if there are errors. Offsite building systems often suffer difficulty if things don't match up exactly right.
Some of the main disadvantages include difficulty in modeling due to inconsistency of the lumber and design complexity. Computer-aided design, modern sawmills, and selective breeding of trees are all working to improve these areas.
In a possible case study, note the productivity of multi-family construction. The first example of a "1+5" stick framed apartment building was in 1996. Building codes have become more friendly to this type of construction. "1+5s" are those 4-5 story rectangular apartment complexes that all look the same, popping up all over growing cities across the US.
There are No Silver Bullets
No cost dominates the cost of new home construction. It is all nickels and dimes:
Framing (green) is the highest cost but far from dominant at 15% of the total. Roughly 50% of the total cost is visible to the consumer - where taste matters. Reducing the cost means finding savings across a wide range of interconnected subsystems and still selling the house.
Improvement Requires Dumbing it Down and Raising our Ambitions
Almost every advancement in construction is small enough for a man to carry: 2x4s, nails, power tools, standard 4'x8' OSB sheathing, 4'x8' drywall, ZIP Sheathing, PEX piping. Each advancement fits within a simple construction system. Any complex attempt at prefab or modular, including by Toyota itself, has failed to reach any significant market share.
Reorganizing Construction is a Hard Way to Win
Prefabbing construction is almost always more expensive than comparable site-built construction. High overhead, capital intensity, and high transportation costs eat away at cost savings. Adoption rates of new technologies are painfully slow. On-site integration can be challenging.
I don't think it is impossible, but the execution has to be almost perfect. Even successes often end up as niche producers arbitraging regulations or labor costs.
General Purpose Technologies (GPTs) Rule
Flexible technologies that work within the current system and simplify processes have had the most success. These technologies allow the high precision and efficiency of factories to make it to the building site. The successful products are small and flexible. Small means they are cheaper to transport or pack efficiently. Flexibility means they can be used over and over on building sites. Adoption drives volumes large enough to justify moving from site-built to factory-built.
Here are some examples:
Experienced carpenters use chisels to create post and beam members on site. -> 2x4s and nails are mass manufactured and assembled by semi-skilled workers on site.
Workers assemble framing with hand saws and hammers. -> Workers use power saws, drills, and pneumatic nail guns to construct framing.
Workers measure individual boards and cut to sheath the framing. -> Workers nail manufactured 4'x8' OSB panels to frame as sheathing and subfloor.
Plumbers measure, cut, and sweat in each piece of copper pipe. -> PEX is unrolled, cut, and pulled into place.
Tyvek house wrap is stapled to OSB sheathing (and often damaged by wind) -> Water barrier is applied to OSB panels in a factory to make ZIP sheathing, reducing site work to taping seams.
Interior walls made of strips of wood and covered in plaster -> Interior walls made of 4'x8' sheets of drywall.
Window frames built on-site and glass installed -> Drop-in modular windows.
Where to Invest
Let's look at where the labor content is. Our ideas have to be able to survive decades-long adoption cycles. The dumber, the better.
The best opportunity is in rough carpentry (framing) labor. I'll give one possible example, a combination of three technologies.
Some companies now precut lumber with a CNC-type machine according to construction drawings. Each piece gets stamped with directions on where it is supposed to go. Currently, workers are constantly measuring, sawing, and using the nail gun. Precut framing means only using the nail gun. The biggest challenge with this is the instructions sent to the cutter have to be correct, or on-site corrections eat efficiency gains. Precut framing is a new twist on an old idea. Sears kit homes consisted of precut framing, but the variation in design was limited. Digitizing the process allows one cutting plant to serve any light wood framing project.
Plans are only partially digitized. Quality of plans and what software engineers refer to as "version control" are not well executed. The software will likely improve over time through trial and error and continued adoption of standards that allow drawings to be interoperable. Any desire to tighten building tolerances and remove "site interpretation" will require better plans.
Most stick-framed designs are over-engineered to compensate for construction defects or poor-quality lumber. "Advanced Framing" is a set of design prescriptions that use better engineering models to reduce the use of wood in framing. Advanced framing also considers electrical, plumbing, and HVAC runs and organizes framing design to reduce installation time. Adoption is low for fear of lowering the safety factor in framing and the need for early coordination with other services. Better plans and precut and labeled lumber could decrease variation in construction, making adoption easier.
These technologies impact $18 per square foot of labor costs and $8 per square foot of material costs.
More ambitious technologies might create more gains:
Invent an extremely high R-value insulation and incorporate it into the sheathing, similar to ZIP-R, which uses foam. Remove the need for interior insulation. Removes $1 in labor plus removes coordination needs between insulation installer, plumbers, and electricians.
Drywall replacement that is a light panel and already pigmented with paint. Bonus points for the ability to be cured on-site to remove seams without taping, mudding, and sanding. Impact: $6.50 per square foot in labor costs, eliminate painting, increased flexibility, and time savings from reducing steps.
Modular electric wiring that is plug-and-play instead of manually installing Romex. Better yet, build nuclear batteries into every appliance and eliminate all wiring. Impact: $4 square foot, reduce steps and complexity.
Reduce plumbing costs by inventing a PEX version of sewer pipes. Flexible and unrolls to reduce installation labor. Replace gas appliances with electric or nuclear versions, eliminate gas piping. Impact: $5 per square foot.
Use the nuclear batteries and improved insulation to move to resistance heating and thermoelectric cooling. Use heat recovery ventilators (HRVs) for air circulation. Eliminate ducting. Impact: $3.50 per square foot and reducing coordination needs.
Roofing and foundations are areas that still need addressing through lighter, cheaper materials.
Full implementation might have cost reductions of 20%-30%. Substantial savings, but not transformational. Houses are complex, with many subsystems that are hard to replace or eliminate. We would need hundreds more ideas like these to get more substantial savings. Getting to a 50% reduction without cheapening finishes would be challenging. A "10x" reduction opportunity requires something like self-assembling nanotech structures. Any savings would likely get rolled into fancier countertops, floors, and fixtures.
Transformational cost reduction would have to come from changing what we think a house is. Imagine you had a thin suit that provided heating, cooling, processed your urine and waste, and kept you clean. Then you could have a house without bathrooms, insulation, heating, cooling, plumbing, and have the electrical eliminated with nuclear batteries. No kitchen because robotic takeout is so cheap. The house could cost $20 per square foot (with low-end finishes) and be smaller. A new home would go up in weeks. The technology is in the bodysuit instead of the house. Bodysuits can be mass-produced and shipped long distances. Ripe for cost reduction. The volumetric value of a home would be even lower.
The Easy Way to Unlock More Low-Cost Housing
How can we provide lower-cost housing today?
Trailers, duplexes, triplexes, or larger multi-family all use stick frame construction. Investment in stick framing compatible GPTs will positively impact these projects.
Trailers already cater to cost-conscious consumers. They are cheap at $50 per square foot. Eliminate the zoning regulations that restrict new trailer parks. Allow buyers to finance trailers as regular real estate. If the government subsidizes 30-year mortgages for well-off buyers, extend the same to trailer buyers. Better yet, remove all that involvement and level the playing field. If trailer sales increased, factories could be more numerous and closer to markets or increase volume, lowering costs.
Rezone to allow more multi-family construction and remove minimum parking requirements. America has some of the cheapest multi-family in the world. We need more of it!
If you think a new building system solves cost or availability, consider how it handles the value density problem and consumer tastes issues.