Scaling CO2 Capture Using Chemical Engineering Heuristics
Quantifying the CO2 Problem
Humans put ~40 billion tons of carbon dioxide into the air each year. Cumulative emissions are ~2.2 trillion tons. It would only take 55 years to return to preindustrial CO2 levels if we went to zero emissions and then captured and buried our current output. Any real-life effort would likely involve some emission reductions paired with capture over a longer time horizon and may not go back to preindustrial levels. We'll assume a capture goal of 40 billion tonnes per year for the cases below.
Things That Work
BASF created the foundation of modern chemical engineering when they commercialized the Haber-Bosch process. There are several important features that almost every world-scale process uses:
-
Liquids > Gases > Solids:
Some fluids and materials are easier to move than others. Liquid pumps are simple, cheap, and reliable. Compressors to move gases are ~10x more expensive than pumps. Solids clump, get stuck, plug, and are abrasive. They cause maintenance mayhem.
-
Continuous Processes over Batch
Modern chemical facilities usually have continuous processes, meaning each plant produces a constant amount of product rather than lumpy batches. The benefits are very similar to the Toyota Production System (they are independent discoveries of the same principles). There is no inventory accumulation within the process, equipment is optimally sized, product velocity through the equipment is high, steady-state conditions reduce variation in product quality, and there is a relentless focus on reliability because any single failure can trip the plant offline.
The move to continuous processes happened naturally because many reactions will not go to completion in a batch reactor. Continuously fed reactors allow for the separation of the product and recycling of the reactant. Chemical engineering doesn't have the same dogma as Toyota because these other benefits were an accident. It is left as "continuous is better" in school. So you'll see a plant with perfect one-piece flow and incredible quality sending its product to giant tank farms or warehouses where there might be months worth of inventory!
-
All About Pipes
Pipe volume increases faster than surface area as diameter increases. It gets cheaper as the size goes up. And the cylinder shape makes a strong pressure vessel that many chemical processes require. Chemical plants are a series of pipes. There is the piping, heat exchangers (little pipes in a big pipe!), reactors, and contact towers.
Another feature is that it is cheap to oversize the pipes. Almost all new plants have much bigger pipe diameters than required, and contact towers are taller than necessary. Plant owners can increase production by upsizing the expensive horsepower (compressors, turbines, pumps) without rebuilding the facility.
A Look At Previous Art
The first ideas to capture CO2 from the air were minor modifications of existing carbon dioxide capture processes used in ammonia plants, refineries, and natural gas processing facilities. Air would be compressed and put through an absorber column using a liquid capture agent (usually an amine). That liquid is heated in a separate recovery tower to release the CO2 and then recycled back into the absorber for more capture. The cost is horrific at ~$1000 per ton of CO2 because the absorber has to be huge to handle all the air and provide the necessary contact area. The amine fluid is also expensive and evaporates, raising costs further.
The next iteration is Carbon Engineering. They modified inexpensive crossflow, forced-draft cooling towers and switched the capture agent to potassium hydroxide. Cooling towers are designed for high airflow to evaporate water. They use fans instead of high-dollar compressors. The hydroxide reacts with carbon dioxide to form potassium carbonate and is the kinetics are good. The downside is that it isn't simple to regenerate potassium carbonate back to potassium hydroxide and CO2. Carbon Engineering has a second mineral loop with lime and limestone, adding complexity and solids handling issues. They think they might get the cost down to $100/ton at scale, which starts to be interesting for chemical production. The air capture component makes up $60/ton of that cost, plus the extra cost it adds to the regeneration step. Air capture is still the dominant cost center.
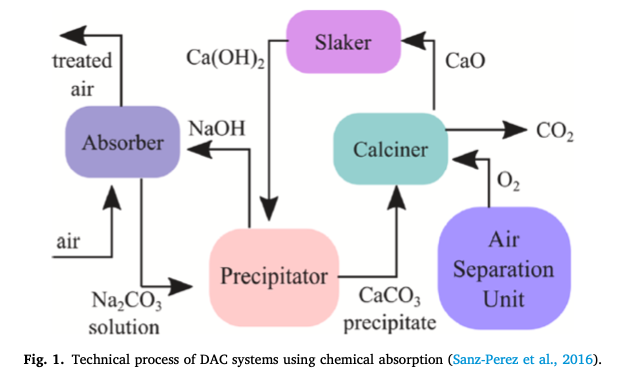
Carbon Engineering's Cycles Source
The Resulting Solution
We need a continuous process that uses liquids in big pipes. The following system is the most extreme version I can think of:
-
Use massive oil storage tanks as air contactors.
Forced draft cooling towers are cheaper than pressurized columns but not cheap enough. Another structure humans can build cheaply is enormous steel storage tanks. They can be over 100 meters in diameter, and their CAPEX decreases as diameter increases, making them ideal at a massive scale. They can be up to 100 meters tall, providing much more volume than forced draft cooling towers like Carbon Engineering uses (~7 meters of contact depth).
-
Use spray columns instead of packing.
Capture happens when carbon dioxide diffuses into liquid and reacts with the capture agent. Most processes use packing, a material with a high surface area per volume. Liquid forms films on the packing surface and maximizes mass transfer and reaction rates. A problem with forced-draft packed cooling towers is that the liquid flow rate is tiny compared to the gas rate. It can be hard to wet the packing adequately or remove dirt. Concern about spraying humans with caustic solutions limits gas velocity and exchanger configurations.
Another option is spray columns. Nozzles create streams of droplets that mix with the air. Advantages include lower capital cost, lower air pressure drop (decreasing fan horsepower), easier cleaning, and no foaming risk. Efficiency can exceed that of packed columns depending on the operating conditions. Companies use these columns to scrub dilute sulfur dioxide from large air flows.
Spray columns are a good fit for our high-volume, low-pressure contactors.
-
Big Fans!
Fans get more efficient as the diameter increases. An example is a low-speed, high-volume fan for livestock barns. A 24' diameter fan moves 9x more air than a 6' fan using 2.5x the power and only weighs twice as much. There is a limit to what is available off the shelf, but wind turbine technology makes giant fans possible.
-
Use cheaper, reversible capture solutions.
Potassium carbonate or sodium carbonate solutions can remove CO2 from the air. Many chemical plants use the Benfield Process with potassium carbonate as the capture agent when the partial pressure of CO2 is high. It receives less attention for air capture because it needs more contact area than amines or hydroxides to capture carbon dioxide. Its advantages are that it is relatively cheap, gives up captured CO2 easily, and has low volatility (preventing evaporation in the air). Capture efficiency is less of a concern if your contact area is cheap because it is made of giant steel cylinders, spray columns, and wind turbine blades.
K2CO3 + H2O + CO2 -> 2KHCO3
2KHCO3 + heat -> H2O + CO2 + K2CO3
-
Traditional Regeneration
Regenerating capture fluid is a normal process similar to any chemical plant using a Benfield System. Decreasing pressure and increasing temperature promote the release of CO2 from the solution. The most cost-effective option is running the regeneration column on a vacuum while heating the fluid. The temperatures are relatively low, usually between 80C and 100C, so any low-grade heat is adequate. There is still a net reduction of carbon dioxide even if fossil fuels provide the heat. A single, massive column could support many air capture tanks. It could be much cheaper than regeneration processes like Carbon Engineering uses.
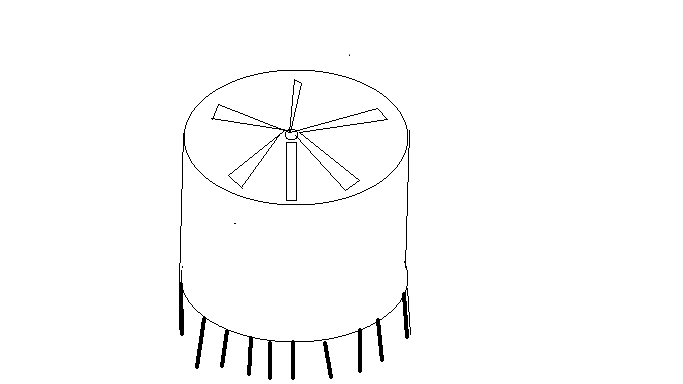
Giant Air Contactors
The engineering is pretty straightforward except for the absorption kinetics, where small changes can make a big difference in performance. Spray columns are less studied than packed columns. Options to overcome the slow kinetics of alkali carbonates are additives, increasing liquid rates, altering droplet size, adjusting spray patterns, or increasing contact volume. Using spray columns would still make Carbon Engineering's process cheaper in a worst-case scenario.
These capture liquids are corrosive to carbon steel when loaded with CO2. Benfield systems usually use corrosion inhibitors (vanadium oxide), but stainless steel or coatings are also an option. Coatings and stainless steel have a relative advantage as the volume of a system increases, but corrosion inhibitors may still win out.
Alkali carbonates react with other acid gases like NOx and SOx. The reactions aren't reversible in the regenerator. So operators must refresh the capture fluid over time. The solutions should get hundreds or thousands of cycles.
The devil is in the details, and this is only a conceptual framework, but it illustrates the power scale has on reducing costs. A variant of this concept could reach a capture cost of $50/ton.
Implications for Climate Change
The proposed solution may not be the cheapest out there. Other ideas like ocean seeding or olivine weathering might be less expensive. But most of the science is understood, and it can scale quickly. I'd guess 100,000 workers could build enough sites to capture our 40 billion tons goal in a decade. The capital expenditure rate would be between $1 trillion and $5 trillion yearly, or 1% to 5% of global GDP. That cost and deployment speed take doomer scenarios off the table. Say something scary like melting permafrost threatens runaway warming. You can target the area with a few years of sulfur cooling while a tiny portion of the global economy builds carbon capture devices. It is nothing like a wartime mobilization.
The most disruptive aspect would be energy usage. We'd need to ramp output up at double-digit rates because each ton of CO2 requires 2-3 MWh of energy for removal. Thankfully low-grade heat is easy to come by. There is enough energy near coal mines in Wyoming or natural gas fields in SW Pennsylvania at less than $5/MWh. Other places might use solar, hydro, or geothermal steam if they lack fossil fuel reserves. The key is to put the facilities at the energy sources instead of trying to move the energy. Cheap energy makes the operating costs <1% of global GDP. Many clean energy proponents have fretted about how to keep fossil fuel reserves in the ground. Burning them to run carbon capture equipment kills two birds with one stone!
The takeaway is that we could completely turn around the carbon dioxide problem within a few years with a similar spending rate as rich world COVID relief. There won't be a scenario where we've waited too long to act.
Point Source Capture
Point source capture is underrated compared to direct air capture. Concentrations of carbon dioxide are much higher, making capture cheaper. Demand for point source carbon capture is limited when carbon is unpriced and there is no CO2-consuming industry nearby. Byzantine permitting for CO2 disposal wells in the US has been an obstacle for a decade. Companies put pure CO2 streams from ethanol plants or ammonia plants into the air instead of underground, even though disposal could be inexpensive.
Many technologies make point source capture cheaper. The most important is burning fuel in pure oxygen. The combustion products are water and carbon dioxide, which are easy to separate. The cost can be much lower than post-combustion capture. The most prominent example is Allam Cycle natural gas power plants. Cement kilns are another promising opportunity.
Direct air capture can remove diffuse emissions and is more flexible in location and size, but there is low-hanging fruit in point source capture.
Manufacturing Scale vs. Construction Scale
Many startups think they can beat chemical engineering by gaining scale through manufacturing volume.
How Manufacturing Can Win
Manufacturing excels at reducing labor and making things that can fit on a truck. Prototypes are cheap, easing startup barriers. Transportation costs can be an issue, especially when the product must be nearly free per cubic meter, like with CO2 capture equipment. We need a different paradigm than liquid capture agents for mass manufacturing.
Most startups with smaller-scale products use solid sorbents. Lime in a box will capture CO2 and is more compact than liquid capture. The solid powder increases reaction surface area while its density is higher than liquid agents. But now solids handling rears its head.
Manufactured designs must be absurdly automated and reliable to keep OPEX in check. The scale of chemical plants also reduces operating labor and maintenance. Process complexity drives the need for operators more than pipe size. A pump that is 10x bigger doesn't need 10x more mechanics. Traditional processing facilities have more flexibility in choosing technology since they can afford 24/7 maintenance and operations coverage.
Another way to fight these scale disadvantages is by taking advantage of market dislocations. Startups like Terraform Industries want to use local, cheap energy (solar) to sell into local product markets (natural gas). Natural gas might be nearly free at the wellhead, but it is pricey once it gets to your house because distribution is expensive. Earning premium prices is critical.
Towards an Optimal Solid Sorbent Design
We need a system that uses solids but must be perfectly automated and reliable. Hard, but not impossible. The best I can come up with after absorbing ideas from the climate/engineering hive mind looks like this:
-
Use sodium carbonate -> sodium bicarbonate as the solid sorbent cycle.
It is cheap, efficient enough at capture, and sodium bicarbonate decomposes at low temperatures (90C-150C depending on how fast you want it to cook).
-
Move the floor, not the material
Augurs, vacuums, slurries, or pressurized air blowers have maintenance and clogging nightmares. We can't afford humans with shovels or dump trucks. The material must be on a linear conveyor belt so it never "moves."
-
Recovery in a Pizza Oven
The low temperature of our mineral cycle means we can move the conveyor belt through something that looks like a Domino's pizza oven for recovery and capture without melting the belt.
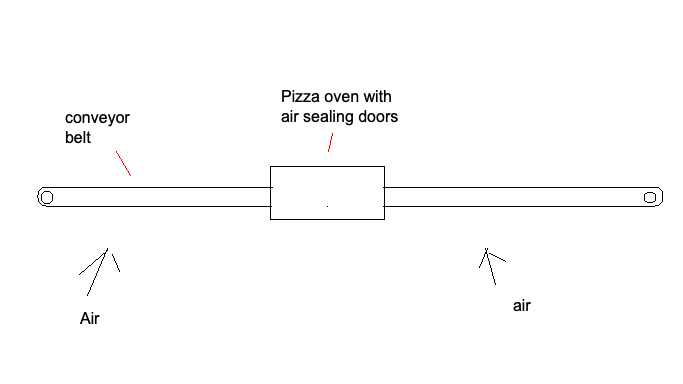
The solid sorbet goes back and forth, back and forth, back and forth, the solid sorbent goes back and forth all week long
It'd be best if the solids never moved, but capture takes orders of magnitude more time than regeneration. Building compartments to handle both capture and regeneration is cost prohibitive. The solution above is a compromise to minimize solids transport while keeping the oven small. A design like this provides a chance for success.
What to do With Carbon Dioxide?
Capture is only the first step.
Inject it Underground
The obvious thing to do is to bury it where it will react with brines and minerals to be locked away forever. One well can handle massive amounts of CO2 injection compared to our capture equipment and is a small cost center. The US government is too strict on disposal well locations and has too much red tape. Things should improve as more states gain primacy over permitting.
CO2 pipelines are expensive because they are usually made of stainless steel to prevent corrosion. Moving the gas skyrockets cost. We should readily put these wells in less-than-perfect locations because they must be close to source facilities to keep costs reasonable. Direct air capture facilities suffer less than point-source capture systems because they can cluster near energy, water, and disposal reservoirs.
Manufacturing Chemicals from CO2
CO2-derived chemicals are a comparative advantage for carbon dioxide capture. They are exciting because capture can happen without government incentives. The catch is that the products must be cheaper than the competition. Many see $100/ton of CO2 as the competitive crossover point.
There are many pathways to producing chemicals, but the theme is that carbon dioxide is stripped of at least one of its oxygens and combined with hydrogen. That can happen directly by combining hydrogen gas and CO2 in a reactor, through growing biomass, or indirectly through processes like CO2 electrolysis. I'm skeptical of biomass approaches because the solid feedstock is diffuse and difficult to process. And I think CO2 electrolysis has a low probability of success after working on it for 18 months[1]. That leaves the direct reaction of hydrogen and carbon dioxide. There are several promising pathways:
-
Methane/Synthetic Natural Gas
Methanation reactions to produce methane from carbon dioxide and hydrogen are well understood, and the conditions are relatively benign. Cost is a challenge because natural gas at the wellhead is cheap. Ultra-cheap electricity from sources like solar PV and exploiting natural gas's high transportation costs provide a chance of success.
CO2 + 4H2 -> CH4 + 2H2O
Electricity will replace many natural gas use cases. Space heating and peak electricity production will be among the most resistant. There is also the possibility of a "lamp oil to gasoline" moment with aerospace companies gaining interest in methane for rocket fuel. Point-to-point suborbital travel over long distances would be the driver of fuel usage.
-
Methanol
Methanol production from hydrogen and CO2 is another well-understood process.
CO2 + 3H2 -> CH3OH + H2O
There are processes to make olefins (plastics precursors) and gasoline from methanol, among others. China already has methanol to olefins facilities with ~1 million tons per year capacities (methanol from coal is cheap!).
We can easily make methanol and turn that into plastics or fuels. Fuels would be carbon-neutral, while plastics sequester carbon when we landfill them. There is no technical risk once you have cheap CO2 and hydrogen.
-
Direct Synthesis of Large Molecules
It is possible to create molecules like ethylene with low selectivity. Turning simple molecules into complex ones becomes an exercise in probability. We can make methane and methanol from hydrogen and CO2 with 98%+ yields because they are single-carbon molecules with simple synthesis paths. Producing more complex molecules involves more steps where intermediates react with each other. Depending how these molecules crash together determines the output. You end up with methane, ethylene, heavier molecules, etc. There are fewer reaction steps but more post-reactor purification costs. Direct synthesis could be competitive but loses more output to less valuable byproducts.
The key that unlocks everything is cheaper CO2 and hydrogen. Cheap hydrogen is the primary limitation because it would allow chemical production from high-quality CO2 sources like ammonia plants. Inexpensive carbon capture provides scale. Most chemical production concepts will require enormous facilities to be feasible. Synthetic natural gas could be an exception because methanation can produce acceptable purity in simple reactors for dispersed customers.
Cheap Hydrogen?
Electrochemistry typically needs special conditions to be successful. Successful processes like Chlor-Alkali (caustic, chlorine), Rowley (magnesium), or Hall-Heroult (aluminum) have much better economics than hydrogen at market prices because they make more valuable products in less electrode area.
Hydrogen's saving grace is that splitting water can happen in a benign environment, like a desk in a middle school classroom. Conditions for the previously mentioned processes are extreme due to temperature or products like chlorine. Splitting water is the default reaction in aqueous electrolysis cells, allowing a wide range of potential catalysts. The product is bubbles of gas, simplifying recovery and purification.
Modern water electrolyzers operate at high pressure to increase performance and provide customers with high-pressure hydrogen. That eliminates plastics as a material of construction. Using metal increases the cost of electrolyzers because most metals corrode in these conditions and only premium alloys are acceptable. The catalysts for the anode and cathode are close together to reduce resistance losses, requiring an expensive membrane to separate each side of the cell. These membranes need ultra-pure water to prevent fouling and only last a limited time. Designers choose costly, efficient catalysts to minimize equipment size. These designs are efficient (~80%) but horrifically expensive.
Cheap hydrogen requires electrolyzers made out of plastic that operate at atmospheric pressure. Very little gas dissolves in solution at atmospheric pressure and typical operating temperatures, allowing the deletion of the membrane. A small amount of electrode spacing, buoyancy, and geometry can keep hydrogen purity at acceptable and safe levels. Cheaper catalyst materials like nickel become competitive as the cost per area drops.
Compression and transportation are expensive because hydrogen has poor volumetric energy density and embrittles metals. It needs to be utilized as a feedstock immediately. Companies might design reactors to operate at lower pressure and handle some stream impurity. Using hydrogen in the wrong context makes it expensive.
The final ingredient is very low-cost electricity. $50/MWh would break even with hydrogen from fossil fuels at 100% efficiency. Our electrolyzers will require electricity at half that price to break even on operating costs! Electricity from solar and wind offer the best hope to reach these costs. Their cost to hook up to electrolyzers is lower than what appears on Lazard's LCOE report because there is less power conversion equipment, and siting doesn't have to account for grid connections. Our cheap electrolyzer takes away some of the sting of lower capacity factors.
US government hydrogen subsidies are so generous that a similar design might make money even if you bought electricity at wholesale grid prices and vented the hydrogen.
Terraform Industries is following this path to make synthetic natural gas. I expect others to follow as interest in hydrogen for chemical feedstock or long-duration energy storage grows.
The Future of Carbon Dioxide Direct Air Capture
Demand for direct air capture depends on government policy, "green" hydrogen prices, the success of point source capture, and the acceptance of more creative sequestration technologies. Government policy might encourage DAC with subsidies or by taxing carbon. The cheaper green hydrogen is, the more competitive chemicals will be. Point source capture is a direct substitute for DAC in providing chemical feedstock and sequestration if it becomes easier to permit wells. Potentially cheaper interventions like mineral weathering can replace carbon sequestration but aren't acceptable chemical feedstock.
The carbon capture method depends heavily on project needs. Burying carbon is method-agnostic, while feedstocks need a certain quality and quantity. Solid sorbents will likely rule for small-scale applications, but traditional methods using big pipes and fans get more competitive as demand increases. Energy availability is also an influence. "Baseload" sources favor traditional methods, while solar PV works better with solid sorbent systems that can concentrate energy use during peak daylight hours.
Cheaper carbon capture encourages government policy and industrial adoption. $1000/ton is a non-starter. Chemicals become competitive at $50-$100/ton while capture and sequestration become cheaper than the cost of pollution. These prices are achievable, and climate change will be just another scare solved by human ingenuity.
- Electrochemistry comes with many constraints and challenges. Using a gas like CO2 as a feedstock only increases them. I've found few paths (if any) that allow production at a reasonable cost. The vast majority of academic research in this space happens under conditions unreasonable for mass production.
The Future of Carbon Dioxide Direct Air Capture
2023 June 13 Twitter Substack See all postsHow do we scale to gigatons? Thanks to Terraform Industries for letting me visit their facility for two days!
Scaling CO2 Capture Using Chemical Engineering Heuristics
Quantifying the CO2 Problem
Humans put ~40 billion tons of carbon dioxide into the air each year. Cumulative emissions are ~2.2 trillion tons. It would only take 55 years to return to preindustrial CO2 levels if we went to zero emissions and then captured and buried our current output. Any real-life effort would likely involve some emission reductions paired with capture over a longer time horizon and may not go back to preindustrial levels. We'll assume a capture goal of 40 billion tonnes per year for the cases below.
Things That Work
BASF created the foundation of modern chemical engineering when they commercialized the Haber-Bosch process. There are several important features that almost every world-scale process uses:
Liquids > Gases > Solids:
Some fluids and materials are easier to move than others. Liquid pumps are simple, cheap, and reliable. Compressors to move gases are ~10x more expensive than pumps. Solids clump, get stuck, plug, and are abrasive. They cause maintenance mayhem.
Continuous Processes over Batch
Modern chemical facilities usually have continuous processes, meaning each plant produces a constant amount of product rather than lumpy batches. The benefits are very similar to the Toyota Production System (they are independent discoveries of the same principles). There is no inventory accumulation within the process, equipment is optimally sized, product velocity through the equipment is high, steady-state conditions reduce variation in product quality, and there is a relentless focus on reliability because any single failure can trip the plant offline.
The move to continuous processes happened naturally because many reactions will not go to completion in a batch reactor. Continuously fed reactors allow for the separation of the product and recycling of the reactant. Chemical engineering doesn't have the same dogma as Toyota because these other benefits were an accident. It is left as "continuous is better" in school. So you'll see a plant with perfect one-piece flow and incredible quality sending its product to giant tank farms or warehouses where there might be months worth of inventory!
All About Pipes
Pipe volume increases faster than surface area as diameter increases. It gets cheaper as the size goes up. And the cylinder shape makes a strong pressure vessel that many chemical processes require. Chemical plants are a series of pipes. There is the piping, heat exchangers (little pipes in a big pipe!), reactors, and contact towers.
Another feature is that it is cheap to oversize the pipes. Almost all new plants have much bigger pipe diameters than required, and contact towers are taller than necessary. Plant owners can increase production by upsizing the expensive horsepower (compressors, turbines, pumps) without rebuilding the facility.
A Look At Previous Art
The first ideas to capture CO2 from the air were minor modifications of existing carbon dioxide capture processes used in ammonia plants, refineries, and natural gas processing facilities. Air would be compressed and put through an absorber column using a liquid capture agent (usually an amine). That liquid is heated in a separate recovery tower to release the CO2 and then recycled back into the absorber for more capture. The cost is horrific at ~$1000 per ton of CO2 because the absorber has to be huge to handle all the air and provide the necessary contact area. The amine fluid is also expensive and evaporates, raising costs further.
The next iteration is Carbon Engineering. They modified inexpensive crossflow, forced-draft cooling towers and switched the capture agent to potassium hydroxide. Cooling towers are designed for high airflow to evaporate water. They use fans instead of high-dollar compressors. The hydroxide reacts with carbon dioxide to form potassium carbonate and is the kinetics are good. The downside is that it isn't simple to regenerate potassium carbonate back to potassium hydroxide and CO2. Carbon Engineering has a second mineral loop with lime and limestone, adding complexity and solids handling issues. They think they might get the cost down to $100/ton at scale, which starts to be interesting for chemical production. The air capture component makes up $60/ton of that cost, plus the extra cost it adds to the regeneration step. Air capture is still the dominant cost center.
Carbon Engineering's Cycles Source
The Resulting Solution
We need a continuous process that uses liquids in big pipes. The following system is the most extreme version I can think of:
Use massive oil storage tanks as air contactors.
Forced draft cooling towers are cheaper than pressurized columns but not cheap enough. Another structure humans can build cheaply is enormous steel storage tanks. They can be over 100 meters in diameter, and their CAPEX decreases as diameter increases, making them ideal at a massive scale. They can be up to 100 meters tall, providing much more volume than forced draft cooling towers like Carbon Engineering uses (~7 meters of contact depth).
Use spray columns instead of packing.
Capture happens when carbon dioxide diffuses into liquid and reacts with the capture agent. Most processes use packing, a material with a high surface area per volume. Liquid forms films on the packing surface and maximizes mass transfer and reaction rates. A problem with forced-draft packed cooling towers is that the liquid flow rate is tiny compared to the gas rate. It can be hard to wet the packing adequately or remove dirt. Concern about spraying humans with caustic solutions limits gas velocity and exchanger configurations.
Another option is spray columns. Nozzles create streams of droplets that mix with the air. Advantages include lower capital cost, lower air pressure drop (decreasing fan horsepower), easier cleaning, and no foaming risk. Efficiency can exceed that of packed columns depending on the operating conditions. Companies use these columns to scrub dilute sulfur dioxide from large air flows.
Spray columns are a good fit for our high-volume, low-pressure contactors.
Big Fans!
Fans get more efficient as the diameter increases. An example is a low-speed, high-volume fan for livestock barns. A 24' diameter fan moves 9x more air than a 6' fan using 2.5x the power and only weighs twice as much. There is a limit to what is available off the shelf, but wind turbine technology makes giant fans possible.
Use cheaper, reversible capture solutions.
Potassium carbonate or sodium carbonate solutions can remove CO2 from the air. Many chemical plants use the Benfield Process with potassium carbonate as the capture agent when the partial pressure of CO2 is high. It receives less attention for air capture because it needs more contact area than amines or hydroxides to capture carbon dioxide. Its advantages are that it is relatively cheap, gives up captured CO2 easily, and has low volatility (preventing evaporation in the air). Capture efficiency is less of a concern if your contact area is cheap because it is made of giant steel cylinders, spray columns, and wind turbine blades.
K2CO3 + H2O + CO2 -> 2KHCO3
2KHCO3 + heat -> H2O + CO2 + K2CO3
Traditional Regeneration
Regenerating capture fluid is a normal process similar to any chemical plant using a Benfield System. Decreasing pressure and increasing temperature promote the release of CO2 from the solution. The most cost-effective option is running the regeneration column on a vacuum while heating the fluid. The temperatures are relatively low, usually between 80C and 100C, so any low-grade heat is adequate. There is still a net reduction of carbon dioxide even if fossil fuels provide the heat. A single, massive column could support many air capture tanks. It could be much cheaper than regeneration processes like Carbon Engineering uses.
Giant Air Contactors
The engineering is pretty straightforward except for the absorption kinetics, where small changes can make a big difference in performance. Spray columns are less studied than packed columns. Options to overcome the slow kinetics of alkali carbonates are additives, increasing liquid rates, altering droplet size, adjusting spray patterns, or increasing contact volume. Using spray columns would still make Carbon Engineering's process cheaper in a worst-case scenario.
These capture liquids are corrosive to carbon steel when loaded with CO2. Benfield systems usually use corrosion inhibitors (vanadium oxide), but stainless steel or coatings are also an option. Coatings and stainless steel have a relative advantage as the volume of a system increases, but corrosion inhibitors may still win out.
Alkali carbonates react with other acid gases like NOx and SOx. The reactions aren't reversible in the regenerator. So operators must refresh the capture fluid over time. The solutions should get hundreds or thousands of cycles.
The devil is in the details, and this is only a conceptual framework, but it illustrates the power scale has on reducing costs. A variant of this concept could reach a capture cost of $50/ton.
Implications for Climate Change
The proposed solution may not be the cheapest out there. Other ideas like ocean seeding or olivine weathering might be less expensive. But most of the science is understood, and it can scale quickly. I'd guess 100,000 workers could build enough sites to capture our 40 billion tons goal in a decade. The capital expenditure rate would be between $1 trillion and $5 trillion yearly, or 1% to 5% of global GDP. That cost and deployment speed take doomer scenarios off the table. Say something scary like melting permafrost threatens runaway warming. You can target the area with a few years of sulfur cooling while a tiny portion of the global economy builds carbon capture devices. It is nothing like a wartime mobilization.
The most disruptive aspect would be energy usage. We'd need to ramp output up at double-digit rates because each ton of CO2 requires 2-3 MWh of energy for removal. Thankfully low-grade heat is easy to come by. There is enough energy near coal mines in Wyoming or natural gas fields in SW Pennsylvania at less than $5/MWh. Other places might use solar, hydro, or geothermal steam if they lack fossil fuel reserves. The key is to put the facilities at the energy sources instead of trying to move the energy. Cheap energy makes the operating costs <1% of global GDP. Many clean energy proponents have fretted about how to keep fossil fuel reserves in the ground. Burning them to run carbon capture equipment kills two birds with one stone!
The takeaway is that we could completely turn around the carbon dioxide problem within a few years with a similar spending rate as rich world COVID relief. There won't be a scenario where we've waited too long to act.
Point Source Capture
Point source capture is underrated compared to direct air capture. Concentrations of carbon dioxide are much higher, making capture cheaper. Demand for point source carbon capture is limited when carbon is unpriced and there is no CO2-consuming industry nearby. Byzantine permitting for CO2 disposal wells in the US has been an obstacle for a decade. Companies put pure CO2 streams from ethanol plants or ammonia plants into the air instead of underground, even though disposal could be inexpensive.
Many technologies make point source capture cheaper. The most important is burning fuel in pure oxygen. The combustion products are water and carbon dioxide, which are easy to separate. The cost can be much lower than post-combustion capture. The most prominent example is Allam Cycle natural gas power plants. Cement kilns are another promising opportunity.
Direct air capture can remove diffuse emissions and is more flexible in location and size, but there is low-hanging fruit in point source capture.
Manufacturing Scale vs. Construction Scale
Many startups think they can beat chemical engineering by gaining scale through manufacturing volume.
How Manufacturing Can Win
Manufacturing excels at reducing labor and making things that can fit on a truck. Prototypes are cheap, easing startup barriers. Transportation costs can be an issue, especially when the product must be nearly free per cubic meter, like with CO2 capture equipment. We need a different paradigm than liquid capture agents for mass manufacturing.
Most startups with smaller-scale products use solid sorbents. Lime in a box will capture CO2 and is more compact than liquid capture. The solid powder increases reaction surface area while its density is higher than liquid agents. But now solids handling rears its head.
Manufactured designs must be absurdly automated and reliable to keep OPEX in check. The scale of chemical plants also reduces operating labor and maintenance. Process complexity drives the need for operators more than pipe size. A pump that is 10x bigger doesn't need 10x more mechanics. Traditional processing facilities have more flexibility in choosing technology since they can afford 24/7 maintenance and operations coverage.
Another way to fight these scale disadvantages is by taking advantage of market dislocations. Startups like Terraform Industries want to use local, cheap energy (solar) to sell into local product markets (natural gas). Natural gas might be nearly free at the wellhead, but it is pricey once it gets to your house because distribution is expensive. Earning premium prices is critical.
Towards an Optimal Solid Sorbent Design
We need a system that uses solids but must be perfectly automated and reliable. Hard, but not impossible. The best I can come up with after absorbing ideas from the climate/engineering hive mind looks like this:
Use sodium carbonate -> sodium bicarbonate as the solid sorbent cycle.
It is cheap, efficient enough at capture, and sodium bicarbonate decomposes at low temperatures (90C-150C depending on how fast you want it to cook).
Move the floor, not the material
Augurs, vacuums, slurries, or pressurized air blowers have maintenance and clogging nightmares. We can't afford humans with shovels or dump trucks. The material must be on a linear conveyor belt so it never "moves."
Recovery in a Pizza Oven
The low temperature of our mineral cycle means we can move the conveyor belt through something that looks like a Domino's pizza oven for recovery and capture without melting the belt.
The solid sorbet goes back and forth, back and forth, back and forth, the solid sorbent goes back and forth all week long
It'd be best if the solids never moved, but capture takes orders of magnitude more time than regeneration. Building compartments to handle both capture and regeneration is cost prohibitive. The solution above is a compromise to minimize solids transport while keeping the oven small. A design like this provides a chance for success.
What to do With Carbon Dioxide?
Capture is only the first step.
Inject it Underground
The obvious thing to do is to bury it where it will react with brines and minerals to be locked away forever. One well can handle massive amounts of CO2 injection compared to our capture equipment and is a small cost center. The US government is too strict on disposal well locations and has too much red tape. Things should improve as more states gain primacy over permitting.
CO2 pipelines are expensive because they are usually made of stainless steel to prevent corrosion. Moving the gas skyrockets cost. We should readily put these wells in less-than-perfect locations because they must be close to source facilities to keep costs reasonable. Direct air capture facilities suffer less than point-source capture systems because they can cluster near energy, water, and disposal reservoirs.
Manufacturing Chemicals from CO2
CO2-derived chemicals are a comparative advantage for carbon dioxide capture. They are exciting because capture can happen without government incentives. The catch is that the products must be cheaper than the competition. Many see $100/ton of CO2 as the competitive crossover point.
There are many pathways to producing chemicals, but the theme is that carbon dioxide is stripped of at least one of its oxygens and combined with hydrogen. That can happen directly by combining hydrogen gas and CO2 in a reactor, through growing biomass, or indirectly through processes like CO2 electrolysis. I'm skeptical of biomass approaches because the solid feedstock is diffuse and difficult to process. And I think CO2 electrolysis has a low probability of success after working on it for 18 months[1]. That leaves the direct reaction of hydrogen and carbon dioxide. There are several promising pathways:
Methane/Synthetic Natural Gas
Methanation reactions to produce methane from carbon dioxide and hydrogen are well understood, and the conditions are relatively benign. Cost is a challenge because natural gas at the wellhead is cheap. Ultra-cheap electricity from sources like solar PV and exploiting natural gas's high transportation costs provide a chance of success.
CO2 + 4H2 -> CH4 + 2H2O
Electricity will replace many natural gas use cases. Space heating and peak electricity production will be among the most resistant. There is also the possibility of a "lamp oil to gasoline" moment with aerospace companies gaining interest in methane for rocket fuel. Point-to-point suborbital travel over long distances would be the driver of fuel usage.
Methanol
Methanol production from hydrogen and CO2 is another well-understood process.
CO2 + 3H2 -> CH3OH + H2O
There are processes to make olefins (plastics precursors) and gasoline from methanol, among others. China already has methanol to olefins facilities with ~1 million tons per year capacities (methanol from coal is cheap!).
We can easily make methanol and turn that into plastics or fuels. Fuels would be carbon-neutral, while plastics sequester carbon when we landfill them. There is no technical risk once you have cheap CO2 and hydrogen.
Direct Synthesis of Large Molecules
It is possible to create molecules like ethylene with low selectivity. Turning simple molecules into complex ones becomes an exercise in probability. We can make methane and methanol from hydrogen and CO2 with 98%+ yields because they are single-carbon molecules with simple synthesis paths. Producing more complex molecules involves more steps where intermediates react with each other. Depending how these molecules crash together determines the output. You end up with methane, ethylene, heavier molecules, etc. There are fewer reaction steps but more post-reactor purification costs. Direct synthesis could be competitive but loses more output to less valuable byproducts.
The key that unlocks everything is cheaper CO2 and hydrogen. Cheap hydrogen is the primary limitation because it would allow chemical production from high-quality CO2 sources like ammonia plants. Inexpensive carbon capture provides scale. Most chemical production concepts will require enormous facilities to be feasible. Synthetic natural gas could be an exception because methanation can produce acceptable purity in simple reactors for dispersed customers.
Cheap Hydrogen?
Electrochemistry typically needs special conditions to be successful. Successful processes like Chlor-Alkali (caustic, chlorine), Rowley (magnesium), or Hall-Heroult (aluminum) have much better economics than hydrogen at market prices because they make more valuable products in less electrode area.
Hydrogen's saving grace is that splitting water can happen in a benign environment, like a desk in a middle school classroom. Conditions for the previously mentioned processes are extreme due to temperature or products like chlorine. Splitting water is the default reaction in aqueous electrolysis cells, allowing a wide range of potential catalysts. The product is bubbles of gas, simplifying recovery and purification.
Modern water electrolyzers operate at high pressure to increase performance and provide customers with high-pressure hydrogen. That eliminates plastics as a material of construction. Using metal increases the cost of electrolyzers because most metals corrode in these conditions and only premium alloys are acceptable. The catalysts for the anode and cathode are close together to reduce resistance losses, requiring an expensive membrane to separate each side of the cell. These membranes need ultra-pure water to prevent fouling and only last a limited time. Designers choose costly, efficient catalysts to minimize equipment size. These designs are efficient (~80%) but horrifically expensive.
Cheap hydrogen requires electrolyzers made out of plastic that operate at atmospheric pressure. Very little gas dissolves in solution at atmospheric pressure and typical operating temperatures, allowing the deletion of the membrane. A small amount of electrode spacing, buoyancy, and geometry can keep hydrogen purity at acceptable and safe levels. Cheaper catalyst materials like nickel become competitive as the cost per area drops.
Compression and transportation are expensive because hydrogen has poor volumetric energy density and embrittles metals. It needs to be utilized as a feedstock immediately. Companies might design reactors to operate at lower pressure and handle some stream impurity. Using hydrogen in the wrong context makes it expensive.
The final ingredient is very low-cost electricity. $50/MWh would break even with hydrogen from fossil fuels at 100% efficiency. Our electrolyzers will require electricity at half that price to break even on operating costs! Electricity from solar and wind offer the best hope to reach these costs. Their cost to hook up to electrolyzers is lower than what appears on Lazard's LCOE report because there is less power conversion equipment, and siting doesn't have to account for grid connections. Our cheap electrolyzer takes away some of the sting of lower capacity factors.
US government hydrogen subsidies are so generous that a similar design might make money even if you bought electricity at wholesale grid prices and vented the hydrogen.
Terraform Industries is following this path to make synthetic natural gas. I expect others to follow as interest in hydrogen for chemical feedstock or long-duration energy storage grows.
The Future of Carbon Dioxide Direct Air Capture
Demand for direct air capture depends on government policy, "green" hydrogen prices, the success of point source capture, and the acceptance of more creative sequestration technologies. Government policy might encourage DAC with subsidies or by taxing carbon. The cheaper green hydrogen is, the more competitive chemicals will be. Point source capture is a direct substitute for DAC in providing chemical feedstock and sequestration if it becomes easier to permit wells. Potentially cheaper interventions like mineral weathering can replace carbon sequestration but aren't acceptable chemical feedstock.
The carbon capture method depends heavily on project needs. Burying carbon is method-agnostic, while feedstocks need a certain quality and quantity. Solid sorbents will likely rule for small-scale applications, but traditional methods using big pipes and fans get more competitive as demand increases. Energy availability is also an influence. "Baseload" sources favor traditional methods, while solar PV works better with solid sorbent systems that can concentrate energy use during peak daylight hours.
Cheaper carbon capture encourages government policy and industrial adoption. $1000/ton is a non-starter. Chemicals become competitive at $50-$100/ton while capture and sequestration become cheaper than the cost of pollution. These prices are achievable, and climate change will be just another scare solved by human ingenuity.