The Old Guard Decays
America's traditional aerospace industry has gone from world dominance to decay.
The Fall of Boeing
Boeing has historically maintained a strong engineering and manufacturing culture. Engineers dominated management, and their office was a short drive to the two most important factories. In the early 1990s, this culture shined as the 777 was on time, on budget, and sold well. By 2004, Boeing moved its C-Suite headquarters to Chicago, made several culture-clashing acquisitions, and hired an outsider MBA as CEO instead of an engineer. The changes separated its management and board from the day-to-day processes at the heart of its business. Alan Mullaly, who led the 777 program, served as CEO of Boeing Commercial Aviation, and later CEO of Ford Motors, described the changes:
In the old days, you would go to the board and ask for X amount of money, and they'd counter with Y amount of money, and then you'd settle on a number, and that's what you'd use to develop the plane. These days, you go to the board, and they say, "Here's the budget for this airplane, and we'll be taking this piece of it off the top, and you get what's left; don't fuck up."
The first product developed under this new regime was the 787, which became one of the most botched aerospace product launches in history.
Amid the 787 debacle, Boeing had to decide whether to replace the 737 with a clean sheet design or another upgrade. The 737 program management strongly favored a clean sheet design because another redesign would be challenging to integrate into the existing 737 airframe. Boeing's management delayed this decision, fearing another 787 debacle. The Chicago C-Suite had lost trust in their engineering teams in Seattle. American Airlines forced their hand when they threatened to place a large order with Airbus unless 737 was improved or replaced. In a panic, Boeing's CEO and board green-lighted the fourth major upgrade to the 737, known as 737 MAX.
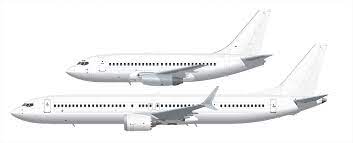
737 Version 1 in 1968 vs. Version 4; Source: Reddit User u/erhue
To accommodate larger engines and further stretching of the plane, the engineers sacrificed stability. They wrote flight control software that compensated for the loss in airworthiness. A cascade of errors led to this system failing in two 737 MAX crashes, killing 346. 737 MAX was grounded for a length of time that severely harmed Boeing's business.
Precision Cast Parts and the Supply Chain
A modern airliner has over 100,000 parts. Each of these parts has rigorous requirements for precision, quality, and regulatory compliance. The number of companies manufacturing these parts has decreased through consolidation.
Precision Castparts (PCC) is the poster child of this consolidation. PCC realized that these niche manufacturers had little competition. They could buy them and raise prices. It would be hard for new entrants to overcome quality and regulatory barriers.
PCC grew until it became a Fortune 500 company. Berkshire Hathaway eventually acquired PCC. Warren Buffet can't resist buying a dominant company in a stodgy, uncompetitive industry. Berkshire Hathaway had to write off part of its investment as the 737 MAX delay ravaged PCC's finances.
Lockheed, Boeing, and ULA
America's space launch business also saw waves of consolidation. By the mid-2000s, the government primarily relied on Boeing and Lockheed for national security and science launches. Each company manufactured a family of rockets (Atlas and Delta) based on ICBMs from the 1960s.
Cost increases meant these programs could no longer compete for commercial launches. Commercial payloads were flying on Russian or European rockets instead. Lockheed and Boeing convinced the government to bless a merger called United Launch Alliance (ULA) to reverse their losses. The government agreed to pay far above market price to maintain this American launch capability and paid flat "launch readiness" payments. ULA would keep both the Atlas and Delta families of rockets (Jobs!).
Both Boeing and Lockheed have kept in-house space businesses that primarily feast on cost-plus government contracts. Boeing's Space Launch System rocket is years overdue and tens of billions over budget.
Boeing did win a fixed-price contract for NASA to build a system to transport astronauts to the International Space Station. Software errors plagued its uncrewed "Demo" launch after Boeing elected to skip a full software integration test to save money. A materials corrosion problem with its hypergolic fuel delayed its second Demo flight.
Boeing submitted a bid for NASA's commercial moon landing system. It did not make it past the first round of proposals. Boeing became enmeshed in a scandal when a NASA employee used back channels to illegally notify them that they needed to update their bid because it was substandard.
The New Guard Emerges and Goes METAL
Since I wrote my post on America's new manufacturing technology and methods, Elon Musk gave us a better version of Tesla and SpaceX's algorithm:
-
Make Requirements Less Dumb
Much of the cost, complexity, and timeline of a project comes from its requirements. It is a truism that requirements are always wrong because some have a higher price than the benefits they provide, especially in complex projects. Spending time to make sure they are reasonable, especially when many departments are involved, is well worth the effort.
-
Delete the Part/Process
Most projects continually add complexity for any new case or requirement. Instead of adding a new part or process, rethink the system to delete steps and reduce complexity.
-
Simplify or Optimize
Only once you are sure something is required do you optimize it.
-
Accelerate Cycle Time
Do it faster!
-
Automate
Automation is capital intensive. Use it once the process is well defined and optimized.
SpaceX
Falcon 9
When SpaceX first designed Falcon 9, it was not easily manufacturable. The company struggled to do several launches in a year and was piling up customers more rapidly than it could launch. There were only five launches between 2010 and early 2013.
Part of the struggle was that existing suppliers were slow and expensive. SpaceX designed and manufactured many of its components to survive. In the several books that detail SpaceX's early years, there are numerous examples of engineers manufacturing a part for a few thousand dollars that might cost hundreds of thousands from a traditional supplier (if it existed).
Performance and manufacturing difficulty improved through several upgrades, culminating with the launch of the first "Block 5" Falcon 9 in 2018. Even though manufacturability had improved, most of the increase in flight rate that Falcon 9 achieved is from reusing first stages and fairings rather than improved manufacturing speed. Falcon 9 has come to dominate the global launch market, carrying ~75% of the tons to orbit in 2021.
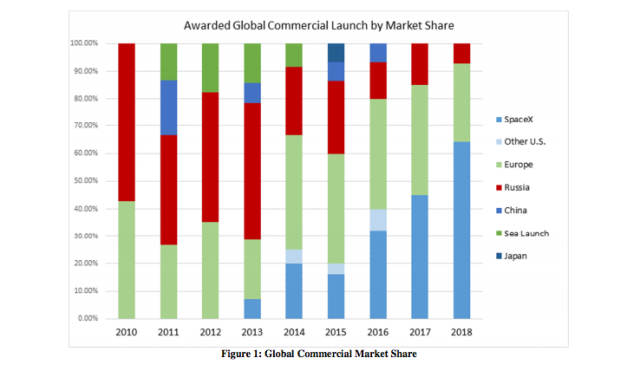
It has only gone up! Source: SpaceX
The Next Generation
SpaceX's mission has always been to get to Mars and take millions of people with them. Falcon 9's cost structure is not capable of achieving that goal.
Musk proposed a line of designs that changed as he learned about manufacturing from Tesla's expansion. The rocket has decreased in size, while the non-engine structure has become simpler.
Engineers design a rocket around its engines. For the Mars rocket, SpaceX developed the holy grail of chemical rocket engines, a full-flow staged combustion engine called Raptor. Neither Russia nor NASA has ever successfully fired a full-flow staged combustion engine on a test stand, let alone flown one. Raptor has features that enhance performance and reusability over traditional rocket engines.
-
Better Turbopumps
Raptor's turbopumps don't require the complicated seals that the Space Shuttle Main Engines do. The full-flow nature of the engine lowers the temperature in the turbopump, extending the cycle life of components. One of the main benefits of full flow is that it does not waste as much fuel powering the turbopumps.
-
Methane Fuel
Methane fuel is clean-burning, preventing soot build-up that kerosene-fueled rockets like Falcon 9 experience. Methane is the simplest fuel to manufacture on Mars.
-
Smaller Rocket Structure
Methane is not the most efficient fuel; hydrogen is. Methane is denser than hydrogen, making the fuel tanks (and rocket) smaller than a hydrogen rocket's structure. A smaller rocket is cheaper and easier to build.
Each ship requires 30-40 raptor engines, and many ships will be built, justifying a mass-production system. It is cheaper to integrate complexity in mass-manufactured engines than in the 40-story building size rocket structure. Designs have evolved to simplify the rocket body and make it easier to build.
-
Carbon Fiber to Stainless Steel Body
At first glance, carbon fiber (CF) is the lightest material to make a rocket. SpaceX went so far as to order carbon fiber tooling and build a test oxygen tank. Its strength-to-weight ratio can be as much as 5x better than steel. But carbon fiber performs best near room temperature. It is brittle at cold temperatures and decomposes at high temperatures. Some stainless steel has the same strength to weight ratio as CF at cryogenic temperatures. Rocket fuel stored at cryogenic temperatures is much denser and makes the rocket more efficient. CF rocket bodies require a heavy heat shield because a rocket reentry generates incredible temperatures. Stainless steel can handle much higher temperatures than CF, reducing heat shield mass. A stainless steel reusable rocket ends up being lighter than a carbon fiber one. Best of all, stainless steel is a fraction of the cost and is easy to use. These are good features when you want to build thousands of rockets as tall as 40 story buildings.
-
Delete the Helium Tanks
Falcon 9 has high-pressure helium tanks that empty into the fuel tank to keep it pressurized as fuel drains during flight. Instead, hot methane or oxygen will pressurize the tanks. The helium tanks were related to both of Falcon 9's failures.
-
Delete the Nitrogen Tanks
Pressurized nitrogen is used in small thrusters to make adjustments to Falcon 9's orientation. Starship will bleed the hot gas from the empty fuel tanks instead, reducing complexity, shrinking rocket landing mass, and reducing required landing fuel mass.
-
Delete the Grid Fin Folding Mechanism
On Falcon 9, grid fins help steer the rocket booster as it comes back to land. The fins fold out when the 1st stage booster starts its return. No one had checked whether the folded-out fins had an impact on launch aerodynamics. The fins are out of the airstream, and SpaceX is removing the folding mechanism on Starship.
A simpler ship, especially the switch to steel, meant a program of rapidly iterating through prototypes emerged. Ships are being built every few weeks, incrementally adding and testing more complexity. They regularly blow up during testing, exposing problems. In complex systems, these problems are almost impossible to pinpoint ahead of time. Elon Musk said in a recent interview that rarely was a failure mode identified in pre-flight "top risks" lists. Spending time trying to reduce failures on paper would target the wrong ones and likely add complexity in solving problems that don't exist.
Starship could reach orbit as soon as 2021.
Traditional vs. Additive Manufacturing
SpaceX's success has encouraged hundreds of startups to pursue the launch market. The two most interesting, with diametrically opposing manufacturing strategies, are Astra and Relativity.
Astra
Astra is trying to design an extremely manufacturable rocket. The goal for launch cadence is daily.
One of the core principles of the company is "Simple Scales." Their rocket is a no-frills design made of easily manufactured materials and components. One example is that they nixed an industry standard of carbon fiber payload fairings because they would be costly. They went with an aluminum fairing that weighs 20% more but reduces part cost and manufacturing time by over 95%.
Like SpaceX, Astra practices aggressive iterative design methodologies and builds most components in-house. Their first several launches had dummy second stages. The iteration allows them to find designs that fly with the lowest cost. They have completed three orbital launch attempts, with the second attempt being only seconds away from achieving orbit. Astra has a good chance of being the fastest privately developed rocket to orbit.
Astra's customers are satellite companies operating Low Earth Orbit constellations for imaging and communications. Because they are launching hundred of identical satellites, Astra realized that reaching a 99.9% success rate was unnecessary. Ignoring war-gamed corner cases and initially targeting 95% success rates would allow development to be faster, lowering costs. Customers might lose 5% of their payloads, but a much lower-cost rocket makes up for them. As launch numbers increase, actual failure modes can be found and corrected. Long-term failure rates may be much lower than linearly designed rockets with low flight rates because those rockets have unneeded complexity that increases possible failure modes.
Long term, Astra wants to manufacture rockets at high volume, where costs fall rapidly. Physics favors big rockets, and economics favors reusability, making it likely that Astra iterates to larger reusable rockets - if they survive.
Relativity Space
Astra avoids 3d printing and dismisses it as slow and expensive. Relativity is building as much of their rocket using 3d printing as possible. Relativity's founders noticed that rockets were essentially hand-built and that labor costs were horrific. 3D printing would reduce manufacturing labor and allow design iterations without changing tooling.
Relativity has built the largest and most advanced 3d printers in the world. It currently takes a few months to print an entire rocket. The 3d printer has appreciably sped up Relativity's engine design and testing cycle because engines print faster. While Astra has launched five prototypes, Relativity has zero launches, even being one year older. It could still be the fastest or second fastest privately developed rocket to orbit if the company meets its schedule.
Relativity's rocket, Terran 1, has somewhere around 10x Astra's payload. Relativity is planning a second rocket, Terran-R, that will deliver over 10x the mass to orbit (20,000 kg, comparable to Falcon 9) than Terran 1 and be completely reusable. It will be a challenge for Relativity to execute on their ambitions.
Outcomes
Astra's rocket costs $2.5 million right now, but a similar ride on a Falcon 9 rideshare is $1 million. Relativity's Terran 1 costs $12.5 million, the competing rideshare costing $7 million. Both companies have large order books because they work on launch customers' timelines and provide optimized orbital insertion, compared to rideshare. There is more launch demand than capacity, so both companies have a short time to bring their costs more in line before Starship comes online.
There are dozens more US launch startups. Many share the story of using iteration to test and design rockets, and they make all their parts in-house. It seems unlikely that more than a few companies emerge alive from this maelstrom. It will be fun to see what happens.
The Not Metal Startups
Rocket Lab's Electron was the second privately funded and operated rocket to make it to orbit (after SpaceX's Falcon 1). While its accomplishments are impressive, it has struggled to increase launch cadence and has suffered several failures. Electron maximizes performance to orbit, but it is hard to build. After realizing how slow scaling production would be, Rocket Lab is attempting to add reusability to their first stage to help improve launch cadence. It is also pursuing a rocket with a 20 times larger payload to better compete with other emerging players.
Blue Origin, funded and owned by Jeff Bezos, is one of the oldest space startups. Founded several years before SpaceX, Blue Origin still has not made it to orbit. The memes are ruthless, including "Jeff Who?" because you aren't anybody if you haven't made it to orbit, and "Where are my engines, Jeff?" because Blue Origin is years late in delivering BE-4 engines to ULA for its Vulcan rocket. Bezos has not participated in the day-to-day and encouraged linear design thinking instead of iterative design using the motto "Step by Step." He later had to change this to "Step by Step, ferociously." The CEO he hired, Bob Smith, runs Blue Origin like Boeing. Bezos is now emphasizing the "ferociously" portion of the motto. Only time will tell if this money pit can turn around.
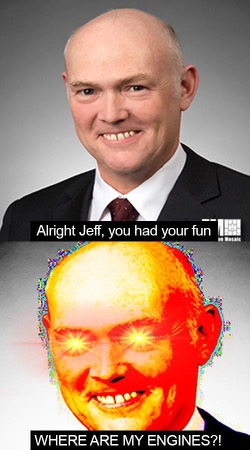
Tory wants to know! Source: Reddit User u/N1ckFl1ghtX
The Next Wave
Many startups have decided to utilize SpaceX's launch costs and capabilities rather than compete with them.
Supply Chain
One theme within our METAL startups is that they are all vertically integrated. It isn't realistic to get to orbit using the existing supply chain.
Hadrian is one of the first of what will likely be many startups that attempt to compete with companies like PCC. Their goal is to halve the cost of building rockets, drones, and other craft by supplying better parts faster and cheaper. This sector is still nascent.
Taking Advantage of Cheap Launch Costs
Other startups realize that lower launch costs allow a range of new businesses.
Earth imagery and monitoring is a burgeoning industry. Planet Labs uses low-cost satellites to image every spot on Earth several times per day for governments, NGOs, and financial data aggregators, among others. Spire collects imagery and weather data from its low-cost constellation for a variety of customers.
Traditional satellite internet uses satellites in Geostationary Orbit (GEO). Satellites in GEO are ~36,000 km away, resulting in latency measured in seconds. The advantage of GEO is one satellite can service a wide area. Low Earth Orbit (LEO) constellations require thousands of satellites because each satellite is only overhead for seconds at a time as it zips around Earth. Low launch costs paired with advancements in phased array antennas allow LEO constellations as low as 550 km orbits, providing latency comparable to terrestrial internet connections. SpaceX's StarLink, OneWeb, and Amazon's Kuiper are a few startups in this space.
Varda Space is one of the most sci-fi startups. They plan to manufacture items in zero gravity that can't be made easily on Earth and return them. Potential products include crystals for better fiber optics, pharmaceuticals, and human organs. They hope to launch within two years, despite barely being a year old.
Defense
For space startups, DOD is one of the biggest customers. Faster, cheaper launch provides capabilities DOD does not have. Satellites are vulnerable to enemy missiles. The old paradigm of obscenely expensive, hand-built satellites and rockets mean space-based imaging and communications evaporate in the first day of near-peer conflict in a barrage of anti-satellite missiles. The new launch startups allow a constant stream of expendable satellites to launch, maintain space-based capabilities, and neutralize the enemy's satellites. Conventional anti-satellite weapons cost more than building and launching micro-satellites.
On Earth, startups like Anduril are building the next generation of aircraft - drones. The advantage of drones is that they are supposed to be cheap enough to be expendable. Drones from traditional defense contractors cost as much as regular aircraft. Anduril is one company that is utilizing modern talent and techniques to build capable, inexpensive drones.
Commercial Air Travel
I recently wrote a post about the emerging technologies in commercial aviation. The summary is that a new wave of small planes is coming from startups (6-20 seats). New technology makes smaller planes as cheap to operate as large commercial airliners while cutting door-to-door travel times. Like the space launch industry, there are dozens of startups, but only a handful will survive.
The New Aerospace Sector
If there ever was an example of Schumpeter's creative destruction, this is it. Traditional aerospace companies have a hoard of capital and talent, providing poor returns to customers. Startups are siphoning the best talent and raising money. Market potential and technology are converging to create an ecosystem that looks more like the aerospace industry pre-1970, including the exploding prototypes, crazy ideas, and swarms of new companies. That aerospace industry took us from the first flight to the moon in ~65 years. The latest batch yearns to take us further.
-
Is SpaceX's Raptor King of the Rocket Engines?, Everyday Astronaut
-
Everyday Astronaut Starbase Tour
-
Eric Berger, Space Reporter
America's Aerospace Industry is Regenerating
2021 August 31 Twitter Substack See all postsA new breed of companies emulates aerospace's golden age.
The Old Guard Decays
America's traditional aerospace industry has gone from world dominance to decay.
The Fall of Boeing
Boeing has historically maintained a strong engineering and manufacturing culture. Engineers dominated management, and their office was a short drive to the two most important factories. In the early 1990s, this culture shined as the 777 was on time, on budget, and sold well. By 2004, Boeing moved its C-Suite headquarters to Chicago, made several culture-clashing acquisitions, and hired an outsider MBA as CEO instead of an engineer. The changes separated its management and board from the day-to-day processes at the heart of its business. Alan Mullaly, who led the 777 program, served as CEO of Boeing Commercial Aviation, and later CEO of Ford Motors, described the changes:
The first product developed under this new regime was the 787, which became one of the most botched aerospace product launches in history.
Amid the 787 debacle, Boeing had to decide whether to replace the 737 with a clean sheet design or another upgrade. The 737 program management strongly favored a clean sheet design because another redesign would be challenging to integrate into the existing 737 airframe. Boeing's management delayed this decision, fearing another 787 debacle. The Chicago C-Suite had lost trust in their engineering teams in Seattle. American Airlines forced their hand when they threatened to place a large order with Airbus unless 737 was improved or replaced. In a panic, Boeing's CEO and board green-lighted the fourth major upgrade to the 737, known as 737 MAX.
737 Version 1 in 1968 vs. Version 4; Source: Reddit User u/erhue
To accommodate larger engines and further stretching of the plane, the engineers sacrificed stability. They wrote flight control software that compensated for the loss in airworthiness. A cascade of errors led to this system failing in two 737 MAX crashes, killing 346. 737 MAX was grounded for a length of time that severely harmed Boeing's business.
Precision Cast Parts and the Supply Chain
A modern airliner has over 100,000 parts. Each of these parts has rigorous requirements for precision, quality, and regulatory compliance. The number of companies manufacturing these parts has decreased through consolidation.
Precision Castparts (PCC) is the poster child of this consolidation. PCC realized that these niche manufacturers had little competition. They could buy them and raise prices. It would be hard for new entrants to overcome quality and regulatory barriers.
PCC grew until it became a Fortune 500 company. Berkshire Hathaway eventually acquired PCC. Warren Buffet can't resist buying a dominant company in a stodgy, uncompetitive industry. Berkshire Hathaway had to write off part of its investment as the 737 MAX delay ravaged PCC's finances.
Lockheed, Boeing, and ULA
America's space launch business also saw waves of consolidation. By the mid-2000s, the government primarily relied on Boeing and Lockheed for national security and science launches. Each company manufactured a family of rockets (Atlas and Delta) based on ICBMs from the 1960s.
Cost increases meant these programs could no longer compete for commercial launches. Commercial payloads were flying on Russian or European rockets instead. Lockheed and Boeing convinced the government to bless a merger called United Launch Alliance (ULA) to reverse their losses. The government agreed to pay far above market price to maintain this American launch capability and paid flat "launch readiness" payments. ULA would keep both the Atlas and Delta families of rockets (Jobs!).
Both Boeing and Lockheed have kept in-house space businesses that primarily feast on cost-plus government contracts. Boeing's Space Launch System rocket is years overdue and tens of billions over budget.
Boeing did win a fixed-price contract for NASA to build a system to transport astronauts to the International Space Station. Software errors plagued its uncrewed "Demo" launch after Boeing elected to skip a full software integration test to save money. A materials corrosion problem with its hypergolic fuel delayed its second Demo flight.
Boeing submitted a bid for NASA's commercial moon landing system. It did not make it past the first round of proposals. Boeing became enmeshed in a scandal when a NASA employee used back channels to illegally notify them that they needed to update their bid because it was substandard.
The New Guard Emerges and Goes METAL
Since I wrote my post on America's new manufacturing technology and methods, Elon Musk gave us a better version of Tesla and SpaceX's algorithm:
Make Requirements Less Dumb
Much of the cost, complexity, and timeline of a project comes from its requirements. It is a truism that requirements are always wrong because some have a higher price than the benefits they provide, especially in complex projects. Spending time to make sure they are reasonable, especially when many departments are involved, is well worth the effort.
Delete the Part/Process
Most projects continually add complexity for any new case or requirement. Instead of adding a new part or process, rethink the system to delete steps and reduce complexity.
Simplify or Optimize
Only once you are sure something is required do you optimize it.
Accelerate Cycle Time
Do it faster!
Automate
Automation is capital intensive. Use it once the process is well defined and optimized.
SpaceX
Falcon 9
When SpaceX first designed Falcon 9, it was not easily manufacturable. The company struggled to do several launches in a year and was piling up customers more rapidly than it could launch. There were only five launches between 2010 and early 2013.
Part of the struggle was that existing suppliers were slow and expensive. SpaceX designed and manufactured many of its components to survive. In the several books that detail SpaceX's early years, there are numerous examples of engineers manufacturing a part for a few thousand dollars that might cost hundreds of thousands from a traditional supplier (if it existed).
Performance and manufacturing difficulty improved through several upgrades, culminating with the launch of the first "Block 5" Falcon 9 in 2018. Even though manufacturability had improved, most of the increase in flight rate that Falcon 9 achieved is from reusing first stages and fairings rather than improved manufacturing speed. Falcon 9 has come to dominate the global launch market, carrying ~75% of the tons to orbit in 2021.
It has only gone up! Source: SpaceX
The Next Generation
SpaceX's mission has always been to get to Mars and take millions of people with them. Falcon 9's cost structure is not capable of achieving that goal.
Musk proposed a line of designs that changed as he learned about manufacturing from Tesla's expansion. The rocket has decreased in size, while the non-engine structure has become simpler.
Engineers design a rocket around its engines. For the Mars rocket, SpaceX developed the holy grail of chemical rocket engines, a full-flow staged combustion engine called Raptor. Neither Russia nor NASA has ever successfully fired a full-flow staged combustion engine on a test stand, let alone flown one. Raptor has features that enhance performance and reusability over traditional rocket engines.
Better Turbopumps
Raptor's turbopumps don't require the complicated seals that the Space Shuttle Main Engines do. The full-flow nature of the engine lowers the temperature in the turbopump, extending the cycle life of components. One of the main benefits of full flow is that it does not waste as much fuel powering the turbopumps.
Methane Fuel
Methane fuel is clean-burning, preventing soot build-up that kerosene-fueled rockets like Falcon 9 experience. Methane is the simplest fuel to manufacture on Mars.
Smaller Rocket Structure
Methane is not the most efficient fuel; hydrogen is. Methane is denser than hydrogen, making the fuel tanks (and rocket) smaller than a hydrogen rocket's structure. A smaller rocket is cheaper and easier to build.
Each ship requires 30-40 raptor engines, and many ships will be built, justifying a mass-production system. It is cheaper to integrate complexity in mass-manufactured engines than in the 40-story building size rocket structure. Designs have evolved to simplify the rocket body and make it easier to build.
Carbon Fiber to Stainless Steel Body
At first glance, carbon fiber (CF) is the lightest material to make a rocket. SpaceX went so far as to order carbon fiber tooling and build a test oxygen tank. Its strength-to-weight ratio can be as much as 5x better than steel. But carbon fiber performs best near room temperature. It is brittle at cold temperatures and decomposes at high temperatures. Some stainless steel has the same strength to weight ratio as CF at cryogenic temperatures. Rocket fuel stored at cryogenic temperatures is much denser and makes the rocket more efficient. CF rocket bodies require a heavy heat shield because a rocket reentry generates incredible temperatures. Stainless steel can handle much higher temperatures than CF, reducing heat shield mass. A stainless steel reusable rocket ends up being lighter than a carbon fiber one. Best of all, stainless steel is a fraction of the cost and is easy to use. These are good features when you want to build thousands of rockets as tall as 40 story buildings.
Delete the Helium Tanks
Falcon 9 has high-pressure helium tanks that empty into the fuel tank to keep it pressurized as fuel drains during flight. Instead, hot methane or oxygen will pressurize the tanks. The helium tanks were related to both of Falcon 9's failures.
Delete the Nitrogen Tanks
Pressurized nitrogen is used in small thrusters to make adjustments to Falcon 9's orientation. Starship will bleed the hot gas from the empty fuel tanks instead, reducing complexity, shrinking rocket landing mass, and reducing required landing fuel mass.
Delete the Grid Fin Folding Mechanism
On Falcon 9, grid fins help steer the rocket booster as it comes back to land. The fins fold out when the 1st stage booster starts its return. No one had checked whether the folded-out fins had an impact on launch aerodynamics. The fins are out of the airstream, and SpaceX is removing the folding mechanism on Starship.
A simpler ship, especially the switch to steel, meant a program of rapidly iterating through prototypes emerged. Ships are being built every few weeks, incrementally adding and testing more complexity. They regularly blow up during testing, exposing problems. In complex systems, these problems are almost impossible to pinpoint ahead of time. Elon Musk said in a recent interview that rarely was a failure mode identified in pre-flight "top risks" lists. Spending time trying to reduce failures on paper would target the wrong ones and likely add complexity in solving problems that don't exist.
Starship could reach orbit as soon as 2021.
Traditional vs. Additive Manufacturing
SpaceX's success has encouraged hundreds of startups to pursue the launch market. The two most interesting, with diametrically opposing manufacturing strategies, are Astra and Relativity.
Astra
Astra is trying to design an extremely manufacturable rocket. The goal for launch cadence is daily.
One of the core principles of the company is "Simple Scales." Their rocket is a no-frills design made of easily manufactured materials and components. One example is that they nixed an industry standard of carbon fiber payload fairings because they would be costly. They went with an aluminum fairing that weighs 20% more but reduces part cost and manufacturing time by over 95%.
Like SpaceX, Astra practices aggressive iterative design methodologies and builds most components in-house. Their first several launches had dummy second stages. The iteration allows them to find designs that fly with the lowest cost. They have completed three orbital launch attempts, with the second attempt being only seconds away from achieving orbit. Astra has a good chance of being the fastest privately developed rocket to orbit.
Astra's customers are satellite companies operating Low Earth Orbit constellations for imaging and communications. Because they are launching hundred of identical satellites, Astra realized that reaching a 99.9% success rate was unnecessary. Ignoring war-gamed corner cases and initially targeting 95% success rates would allow development to be faster, lowering costs. Customers might lose 5% of their payloads, but a much lower-cost rocket makes up for them. As launch numbers increase, actual failure modes can be found and corrected. Long-term failure rates may be much lower than linearly designed rockets with low flight rates because those rockets have unneeded complexity that increases possible failure modes.
Long term, Astra wants to manufacture rockets at high volume, where costs fall rapidly. Physics favors big rockets, and economics favors reusability, making it likely that Astra iterates to larger reusable rockets - if they survive.
Relativity Space
Astra avoids 3d printing and dismisses it as slow and expensive. Relativity is building as much of their rocket using 3d printing as possible. Relativity's founders noticed that rockets were essentially hand-built and that labor costs were horrific. 3D printing would reduce manufacturing labor and allow design iterations without changing tooling.
Relativity has built the largest and most advanced 3d printers in the world. It currently takes a few months to print an entire rocket. The 3d printer has appreciably sped up Relativity's engine design and testing cycle because engines print faster. While Astra has launched five prototypes, Relativity has zero launches, even being one year older. It could still be the fastest or second fastest privately developed rocket to orbit if the company meets its schedule.
Relativity's rocket, Terran 1, has somewhere around 10x Astra's payload. Relativity is planning a second rocket, Terran-R, that will deliver over 10x the mass to orbit (20,000 kg, comparable to Falcon 9) than Terran 1 and be completely reusable. It will be a challenge for Relativity to execute on their ambitions.
Outcomes
Astra's rocket costs $2.5 million right now, but a similar ride on a Falcon 9 rideshare is $1 million. Relativity's Terran 1 costs $12.5 million, the competing rideshare costing $7 million. Both companies have large order books because they work on launch customers' timelines and provide optimized orbital insertion, compared to rideshare. There is more launch demand than capacity, so both companies have a short time to bring their costs more in line before Starship comes online.
There are dozens more US launch startups. Many share the story of using iteration to test and design rockets, and they make all their parts in-house. It seems unlikely that more than a few companies emerge alive from this maelstrom. It will be fun to see what happens.
The Not Metal Startups
Rocket Lab's Electron was the second privately funded and operated rocket to make it to orbit (after SpaceX's Falcon 1). While its accomplishments are impressive, it has struggled to increase launch cadence and has suffered several failures. Electron maximizes performance to orbit, but it is hard to build. After realizing how slow scaling production would be, Rocket Lab is attempting to add reusability to their first stage to help improve launch cadence. It is also pursuing a rocket with a 20 times larger payload to better compete with other emerging players.
Blue Origin, funded and owned by Jeff Bezos, is one of the oldest space startups. Founded several years before SpaceX, Blue Origin still has not made it to orbit. The memes are ruthless, including "Jeff Who?" because you aren't anybody if you haven't made it to orbit, and "Where are my engines, Jeff?" because Blue Origin is years late in delivering BE-4 engines to ULA for its Vulcan rocket. Bezos has not participated in the day-to-day and encouraged linear design thinking instead of iterative design using the motto "Step by Step." He later had to change this to "Step by Step, ferociously." The CEO he hired, Bob Smith, runs Blue Origin like Boeing. Bezos is now emphasizing the "ferociously" portion of the motto. Only time will tell if this money pit can turn around.
Tory wants to know! Source: Reddit User u/N1ckFl1ghtX
The Next Wave
Many startups have decided to utilize SpaceX's launch costs and capabilities rather than compete with them.
Supply Chain
One theme within our METAL startups is that they are all vertically integrated. It isn't realistic to get to orbit using the existing supply chain.
Hadrian is one of the first of what will likely be many startups that attempt to compete with companies like PCC. Their goal is to halve the cost of building rockets, drones, and other craft by supplying better parts faster and cheaper. This sector is still nascent.
Taking Advantage of Cheap Launch Costs
Other startups realize that lower launch costs allow a range of new businesses.
Earth imagery and monitoring is a burgeoning industry. Planet Labs uses low-cost satellites to image every spot on Earth several times per day for governments, NGOs, and financial data aggregators, among others. Spire collects imagery and weather data from its low-cost constellation for a variety of customers.
Traditional satellite internet uses satellites in Geostationary Orbit (GEO). Satellites in GEO are ~36,000 km away, resulting in latency measured in seconds. The advantage of GEO is one satellite can service a wide area. Low Earth Orbit (LEO) constellations require thousands of satellites because each satellite is only overhead for seconds at a time as it zips around Earth. Low launch costs paired with advancements in phased array antennas allow LEO constellations as low as 550 km orbits, providing latency comparable to terrestrial internet connections. SpaceX's StarLink, OneWeb, and Amazon's Kuiper are a few startups in this space.
Varda Space is one of the most sci-fi startups. They plan to manufacture items in zero gravity that can't be made easily on Earth and return them. Potential products include crystals for better fiber optics, pharmaceuticals, and human organs. They hope to launch within two years, despite barely being a year old.
Defense
For space startups, DOD is one of the biggest customers. Faster, cheaper launch provides capabilities DOD does not have. Satellites are vulnerable to enemy missiles. The old paradigm of obscenely expensive, hand-built satellites and rockets mean space-based imaging and communications evaporate in the first day of near-peer conflict in a barrage of anti-satellite missiles. The new launch startups allow a constant stream of expendable satellites to launch, maintain space-based capabilities, and neutralize the enemy's satellites. Conventional anti-satellite weapons cost more than building and launching micro-satellites.
On Earth, startups like Anduril are building the next generation of aircraft - drones. The advantage of drones is that they are supposed to be cheap enough to be expendable. Drones from traditional defense contractors cost as much as regular aircraft. Anduril is one company that is utilizing modern talent and techniques to build capable, inexpensive drones.
Commercial Air Travel
I recently wrote a post about the emerging technologies in commercial aviation. The summary is that a new wave of small planes is coming from startups (6-20 seats). New technology makes smaller planes as cheap to operate as large commercial airliners while cutting door-to-door travel times. Like the space launch industry, there are dozens of startups, but only a handful will survive.
The New Aerospace Sector
If there ever was an example of Schumpeter's creative destruction, this is it. Traditional aerospace companies have a hoard of capital and talent, providing poor returns to customers. Startups are siphoning the best talent and raising money. Market potential and technology are converging to create an ecosystem that looks more like the aerospace industry pre-1970, including the exploding prototypes, crazy ideas, and swarms of new companies. That aerospace industry took us from the first flight to the moon in ~65 years. The latest batch yearns to take us further.
Is SpaceX's Raptor King of the Rocket Engines?, Everyday Astronaut
Everyday Astronaut Starbase Tour
Eric Berger, Space Reporter